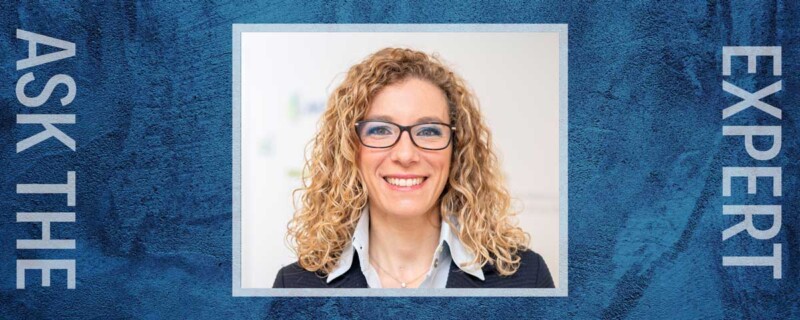
Achieving Large-Scale GMP Viral Vector Manufacturing
Achieving Large-Scale GMP Viral Vector Manufacturing – [Webinar Available On Demand]
As increasing numbers of gene therapies progress through clinical trials and toward commercialization, the need to increase the scale of viral vector manufacturing has become imperative. Key to this effort is improving current manufacturing processes and aligning them with GMP commercial processes. The industry has anticipated this need and has created technologies to support this transition including fit-for-purpose equipment to support platform processes.
We were fortunate to be able to talk with Margherita Neri, Director of Process Development, Milan Site at AGC Biologics about the company’s work in large-scale viral vector manufacturing. In the following interview, Margherita provided insights into the development of their AAV and LV platforms and the successful implementation of the iCELLis™ bioreactor system.
While the live webinar has passed, you can still access the recorded session, “Bridging the Distance to Large-Scale GMP Manufacturing of Viral Vectors,” to learn more about the pioneering work by AGC Biologics in this field.
Can you talk a little about AGC Biologics and your AAV and LV platform processes?
At AGC Biologics we developed ready- to- use platforms for the manufacturing of LVV and AAV both in adhesion and in suspension, called BravoAAV™ and ProntoLVV™. Our platform approach allows us to move from the sequence of the gene of interest to the GMP manufacturing of the first vector batch in less than one year and gives developers a way to standardize their vector development and manufacturing to meet any stage, pre-clinical through commercial.
Why are platform processes important to furthering the cell and gene therapy industry?
The first and most important thing to consider is platform processes reduce the time to GMP, which means accelerating the availability of potentially life-saving treatments to patients. For the developers bringing these therapies to these patients, a platform approach gives them a validated process that they can use. They simply bring their gene of interest, and the AGC Biologics platform developed by our team of experts can help them reach their clinical goals, and beyond.
How did you incorporate iCELLis bioreactor systems in your platforms?
Our BravoAAV™ platform utilizes a 333m² packed bed that allows us to obtain 480L of bulk vector for released serotypes. For lentivirus, we developed our ProntoLVV™ with a 133m² packed bed to obtain 200L of bulk vector. We are now working on increasing the packed bed area to 500m² for both vectors to reach 750L of bulk.
You are going to be presenting a webinar – Bridging the Distance to Large-Scale GMP Manufacturing of Viral Vectors. Can you tell us a bit about what attendees will learn?
Attendees will learn the methodologies for generating reliable process charts for lentivirus and AAV productions. I will share how to enhance virus productivity by upscaling with the iCELLis bioreactor systems. Lastly, we will discuss methods for evaluating product quality by measuring potency and impurities profiles.
To watch:
Bridging the distance to large-scale GMP manufacturing of viral vectors
Presenter: Margherita Neri, Director of Vector Process Development, AGC Biologics
Moderator: Andrew Laskowski, Global Product Manager, Bioreactors, Cytiva