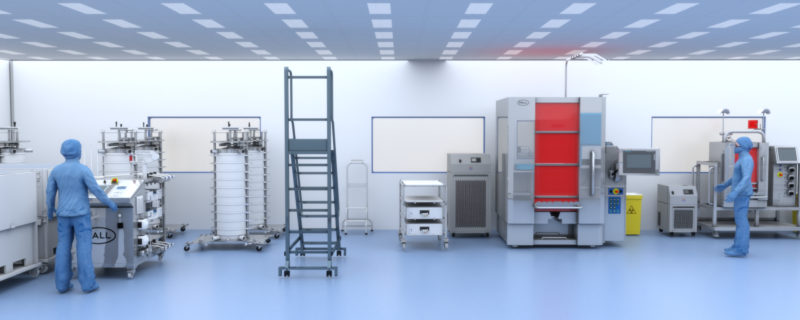
Integrated Solutions to Support Gene Therapy Commercialization
The first approvals in the US for the pioneering Chimeric Antigen Receptor T Cell (CAR T) cell therapies for cancer in 2017 initiated a wave of investment and interest for cell and gene therapies across the industry. There are currently thousands of global cell and gene therapy clinical trials underway, with an increasing proportion of candidates advancing to Phase III clinical evaluation. As momentum in the industry builds and the therapeutic success of cell and gene therapies continue to prove out in clinical trials, the global gene therapy market and investment in this space has likewise grown significantly. As a result, many companies are looking toward manufacturing and commercialization of their lead therapies. However, the path to commercialization for this relatively new modality is not well established and there are still challenges in order to manufacture these products consistently, at the appropriate scale, and cost effectively.
In the white paper, Move Your Gene Therapy from Strategy to Reality, Matt Niloff, Director, Integrated Solutions, and Brandy Sargent, Editor in Chief, Cell Culture Dish and Downstream Column, take an in-depth look at the major manufacturing decisions that companies make in their journey to commercial manufacturing. Gene therapy commercialization focuses on managing and balancing risk during decision making. There are many choices to be made in the clinical, financial, and manufacturing domains, and getting all of these to work together cohesively can be a significant challenge. Should you outsource manufacturing to a CDMO? Invest in in-house manufacturing capabilities? Regardless of the choice, implementing integrated solutions can provide manufacturing systems that work in concert to create a closed, automated, scalable, and performance-qualified network of unit operations. Factors such as the product’s process, scale, automation needs, process economics and manufacturing timelines, will be important in selecting a best-fit manufacturing solution.
Manufacturing for Commercialization
Most gene therapies in development utilize viral vectors to deliver the therapeutic gene into the target cells with transient transfection of mammalian cell lines being the most common method of making virus. There is currently no “one size fits all” manufacturing approach that can encompass the diversity of vectors and cell lines in use and these processes are often plagued by inefficiencies and low yields. Gene therapies also require specialized equipment and bioprocessing knowledge for manufacturing. The demand for these specialized skills brings with it the risk of a shortage of trained personnel in this area. To help meet additional skilled personnel needs, in person courses and e-learning is becoming more readily available at training centers such as BioCentriq™ and Biofactory Competence Center, along with digital training tools hosted by suppliers such as Pall Corporation®.
Integrated Solutions
Being first to market is essential for most gene therapies to maximize the chances of commercial success. Thus, manufacturing processes must be designed early on the path to commercialization. An integrated solution ensures that all unit operations in a manufacturing process are harmonized in the project quoting and execution phases, and that the consumables are appropriately specified and qualified for their intended function. This allows for a reproducible process, and if the incoming raw materials are well controlled, there is a high level of assurance that the process will run at optimal productivity routinely. An experienced and knowledgeable integrated solutions partner can provide the necessary expertise to support these goals and, in turn, shorten time to market.
Implementing Integrated Solutions
Successful implementation of integrated solutions requires a great deal of experience and a deep understanding of manufacturing processes, equipment, automation, and engineering. The most efficient way to access this experience is to work with an end-to-end solutions provider with skilled process experts and end-to-end project management. An integrated solution approach can provide better process economics, risk mitigation and shorter timelines, to maximize the chance for overall project success. However, to achieve this, the right partner must be selected. A good partner should be able to manage the entire project from start to finish and allow the developer time to focus on other critical tasks. They should also be able to design and install equipment, as well as other important aspects such as process design, development, validation, and regulatory support for single-use technologies. A knowledgeable partner should be able to provide validation documentation for the single-use technologies adopted by the users, which meets industry guidelines and is easily accessible via a digital portal.
Leveraging Pall’s AcceleratorSM Integrated Solutions Program
Pall utilizes its Accelerator Integrated Solutions program to help developers and contract development and manufacturing organizations (CDMOs) secure speed to market using robust manufacturing platforms as a starting point. The team at Pall, backed by extensive bioprocess expertise and a diverse equipment and consumables portfolio, can walk their partners through every step of the process. Pall provides a streamlined, integrated approach that includes engineering, process scale-up and project management services.
Pall’s Accelerator Integrated Solutions begins with a robust and highly configurable platform process, such as those for AAV, lentiviral, adenovirus or mRNA. The platform can then be tailored to meet specific process requirements. Pall’s philosophy is to use a collaborative approach to create an appropriately considered and designed integrated solution, which meets customers’ needs within the target timeline and budget. Furthermore, if companies need help to optimize and scale up their processes, Pall’s Process Development services are available to lend their expertise. Such services can bridge a small-scale process with the manufacturing scale integrated solution, thereby reducing start-up time and risk. In addition, Pall has an extensive product portfolio to draw from for manufacturing.
The Accelerator vision software allows an interactive and virtual reality view of facility design. In the white paper, visual examples of how the Accelerator Vision Platform has been used to layout an AAV adherent and an AAV suspension manufacturing process are provided. This software permits full visualization of the process with the capability of optimizing workflow and maximizing operator efficiency.
Also included in the white paper is a real-world example of an integrated end-to-end gene therapy manufacturing solution. Pall Corporation recently partnered with Exothera, a viral vector CDMO, to expand their manufacturing capabilities by adding a large-scale suspension based AAV manufacturing platform, from upstream through to downstream processing of viral vectors of up to 2000 L.
In Summary
Gene therapies have immense potential to revolutionize modern medicine by offering the chance to cure, rather than just treat disease. However, commercial manufacturing and delivering these therapies at a cost that makes them economically feasible can be a challenge. As such, it is important to have a comprehensive understanding of all available manufacturing options so companies can select one that best fits their needs. Leveraging integrated solutions providers like Pall offers a streamlined and accelerated approach to achieving a robust and scalable manufacturing process that can support efficient and cost-effective production that will ultimately broaden patient access to these novel therapies.