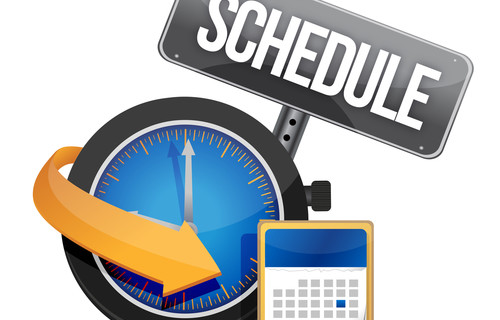
Interactive Scheduling is Key to Successful Biomanufacturing Operations
Biomanufacturing is a complex and hard to manage process that requires the ability to respond to multiple variables. Biomanufacturing planners and schedulers must consider various crucial factors including specialized labor needs, required manufacturing resources, juggling timelines, and unexpected delays when creating manufacturing schedules.
Background
Many biopharmaceutical companies approach manufacturing scheduling by using a traditional scheduling approach, which requires planners meet regularly to discuss and effectively manage the many tasks involved in each step of manufacturing. These tasks are then communicated to a scheduler who coordinates these activities and publishes an operating schedule. The schedule is then provided to shift supervisors at morning coordination meetings. The schedules are often emailed or provided in Excel to shift supervisors, but are static, in that there is no ability to adjust these schedules in real time or provide input from the manufacturing floor based on daily events. The schedule is then communicated to manufacturing employees and operators by posting it electronically or on a whiteboard. At this point, manufacturing is supposed to operate according to the schedule, but these schedules do not take into account issues that arise and quickly render the schedule out of date.
I recently had the pleasure of attending a webinar that addressed these scheduling challenges. The webinar, “Making it Personal,” Driving Accountability in Biomanufacturing was hosted by Bio-G (Bioproduction Group) and provided valuable insight from their experience developing tools to help biopharmaceutical companies manage their manufacturing operations.
Why Traditional Scheduling Doesn’t Work
Bio-G began the webinar by sharing a case study that occurred with one of their biopharmaceutical clients and highlighted the difficulty with current planning and scheduling protocols, including how they quickly become plagued with issues and delays. The case study began with the planning and scheduling meetings that I described above, however in the real life example, someone went home sick and from that one act, a chain reaction of delays ensued. The primary cause of the series of delays stemmed from the lack of communication about problems in real time due to standard communication challenges that included unread emails, meetings, and shift changes. As a result, information about what was happening on the manufacturing floor wasn’t communicated with the next shift or with the scheduler in a timely manner. After the operator went home, his piece of the scheduled tasks didn’t get completed. Once it was discovered that these activities weren’t completed, a series of emails were sent, however due to meetings, shift changes, and other factors, the information did not reach the scheduler before she left for the day. The schedule wasn’t updated until the morning, but by that time, clean hold times had expired, causing further delay. In this case, Bio-G explained that the communication breakdown resulted in a 7.5 hour delay in the manufacturing process with expediting and overtime needed to catch up.
Most people who work in manufacturing can identify with these scheduling issues and subsequent delays, so what can be learned from the case study and why is this type of scheduling ineffective? Bio-G described how the real issue is that no one was clear exactly what tasks were to be performed and who was responsible for them. In short, there was no visibility or personal accountability. To elaborate on that point, there was no integrated communication, which means challenges on the floor were not reported real time and schedules were not updated quickly enough to avoid delays.
A fundamental problem of this traditional approach is that schedulers create the schedule, but they can’t see and respond quickly to events happening on the manufacturing floor.
A New Approach – Tools to Enable Interactive Scheduling and Personal Accountability
Bio-G’s approach to scheduling requires real time feedback from the manufacturing floor, which enables real time schedule updates. Planners and schedulers use the Bio-G software to set the schedule, but others including management, shift supervisors and operators use a calendaring program, like Microsoft Outlook or Exchange, to view the schedule. Bio-G software publishes simultaneously to the company’s existing calendaring program, resulting in several benefits, including:
- More accurate schedules -Bio-G Software pulls in information from historical data collection software to give accurate information on how long a task takes to complete. Using historical information to inform schedules provides a much more accurate estimate of how long to schedule for each event, thus creating a schedule that has realistic timelines.
- Schedule is published directly to employee devices -The scheduler then creates the schedule and publishes it directly to smart phones, tablets, laptops and display boards to provide a real time view—no more white boards or static schedules. The software publishes directly to the company’s existing calendaring system, which employees are already used to using.
- Real time updating of the schedule -If there are problems or delays in manufacturing, these issues can be communicated quickly. Manufacturing employees can make notes and adjust schedule times as proposed changes. Schedulers can then accept or reject these changes and can update schedules real time.
- Improved visibility across the organization – Employees can subscribe to multiple calendars with proper security. For example, downstream can see the calendar for upstream, so they can be aware of any delays on the horizon and downstream schedules can be adjusted. That way, time is not wasted waiting on material that isn’t arriving.
- Increased personal accountability –Shift supervisors are able to allocate detailed work to individuals or teams and publish those tasks to employee’s calendars on their electronic devices. Thus increasing personal accountability and team accountability. To use the case study example, with Bio-G’s program, if someone went home early, the entire team would have been able to see what work they had been tasked with and the work could have been quickly reallocated.
The benefits of this type of integrated scheduling from a management perspective include:
- Improved efficiency – One example given during the webinar was that once integrated scheduling was implemented, the need for coordinating meetings was reduced because there was real-time communication through the schedule and as a result everyone knew what needed to be done without the need for additional meeting time.
- Reduction in manufacturing delays – When an issue arises, it can be caught early to avoid or lessen further delays.
- Productivity increases – Dramatic improvements in worker productivity and adverse event response times.
To Learn More:
Webinar
If you would like to learn more about Bio-G’s tools for scheduling management, please see their webinar “Making it Personal,” Driving Accountability in Biomanufacturing.
2-Day Workshops
Bio-G is also hosting 2-Day workshops around the country on Modeling and Simulation in Biomanufacturing Operations. Attendees work in hands-on sessions with the Bio-G Real-Time Modeling System (RTMS) to solve challenging manufacturing problems, including:
- Modeling and Optimization
- Production Planning and Scheduling
- Cycle Time Reduction and Debottlenecking
- Capacity Analysis
- Analysis of Utilities and Waste Streams
For more information on the 2-Day Workshops, including cities and dates, go to http://www.bio-g.com/post/2-day-workshops.
About Bio-G
Bio-G runs the fastest discrete event simulation software on biomanufacturing operations. They have modeled more than 20% of the world’s biomanufacturing capacity including some of the world’s largest facilities and complex processes like perfusion. They use three toolsets that cover the entire process including product development, commercial manufacturing, API manufacturing and Fill/Finish.
The toolsets include:
- Real-time modeling – de-bottlenecking, real-time scheduling, capacity engineering and long/short team forecasting
- Crosswalk – Real time data consolidation, visualization and analysis
- Biofit – Facility fit, tech transfer, and evaluation of unit operation constraints