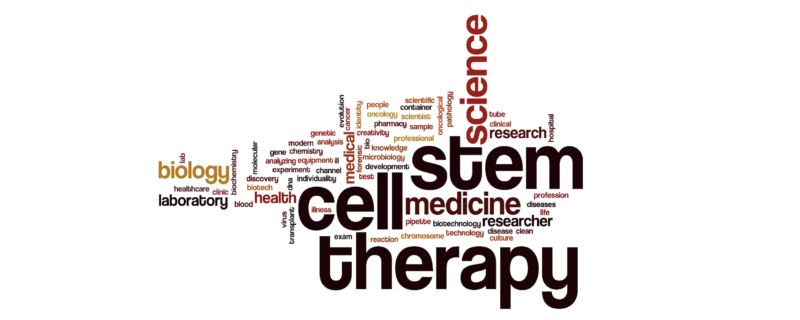
Manufacturing and Qualification Challenges for Cell and Gene Therapy Products and Best Practices for Success
As a growing number of cell and gene therapies (CGTs) advance through clinical trials toward approval, the industry is striving to establish robust and well-characterized biomanufacturing processes. Raw materials for CGT manufacturing must comply with regulatory requirements, including GMP and other quality standards. Variability in raw materials can lead to numerous issues, leading to underperformance and batch failures. BioLegend experts discuss these challenges and how end-to-end GMP solutions are among best practices to yield safe and successful products.
Cell and Gene Therapy Landscape
Cell and gene therapy, or advanced therapy medicinal products (ATMPs) as they are referred to in the EU, represent intersecting categories of biotherapeutics for treating human diseases. Where cell therapy works by infusing cells into a patient to replace or repair damaged or diseased tissue, gene therapy treats the disease at the genetic level. Some gene therapies replace or turn off defective genes, while others introduce new genes to treat or cure a disease. Gene-modified cell therapies, such as chimeric antigen receptor (CAR)-T cells, are considered both cell and gene therapies. Cells from a patient (autologous) or a healthy donor (allogeneic) are genetically engineered ex vivo before the modified cells are infused into a patient for treatment.
Compared to conventional drugs, these “living pharmaceuticals” pose different manufacturing challenges, such as inherent donor variability, cell heterogeneity, insufficient scalability, and batch-to-batch discrepancies. Raw materials play an important, early role in controlling the overall quality, safety, and efficacy of the final products. Raw materials in the context of this discussion are defined as reagents, solvents, substances, or components used in the manufacturing process but not intended to be part of the final therapeutic product1. The list is long, but includes antibodies, cell culture reagents, growth factors, cytokines, and more.
Raw materials made under Good Manufacturing Practice (GMP) are essential to produce safe and effective CGTs. However, there are several challenges faced by biomanufacturers with respect to the raw material qualification process. These challenges are exacerbated by the lack of global standardization, which necessitates a risk-based approach to ensure success. CGT biomanufacturers can reap significant benefits by choosing a reliable and competent supply partner from the outset. This not only ensures raw material quality, but secures a robust and scalable supply chain to meet evolving needs and regulations.
Raw Material Qualification Challenges
Establishing control over raw materials early on is an important aspect of process development, characterization, and commercialization to ensure the final CGT product is effective and safe for patient use. As such, raw material testing is required to confirm the identity and integrity of the material; this ensures that the right product has been received and that it meets the specifications established for its intended use before being released for the manufacturing process2. However, there are other raw material considerations and challenges that biomanufacturers must address to ensure success.
Consistency and Quality
Qualifying raw materials for CGT manufacturing is critical to achieve quality and consistency in the final product. But this can be especially difficult if the materials are derived from biological sources where lot-to-lot variability is common and can lead to numerous issues. Failure to properly address variability can result in underperformance and batch failures.
Scalability
A robust and scalable supply of high-quality raw materials is necessary for large-scale production of the final CGT product. While research-grade raw materials may be used to develop processes in the early developmental stage, regulatory authorities will require the use of GMP materials to ensure patient safety once the first-in-human and clinical testing begins. As it is very difficult to introduce changes in the process at later stages, it is important to carefully evaluate the suitability of each raw material early on2,3.
Regulatory Compliance
Raw materials for CGT manufacturing must comply with regulatory requirements, including GMP and other quality standards. This can be a challenge, particularly in cases where the regulatory requirements are evolving or where there is a lack of clear guidance. On top of that, there is a lack of governance and consistency surrounding the labeling of raw materials where a variety of terminology for raw material quality can be used. For instance, the terms ‘chemically-defined’, ‘xeno-free’, ‘biological-free’, ‘TSE/BSE-free’, and ‘animal component-free’ are often used by suppliers for marketing purposes, making it difficult for biomanufacturers to properly evaluate the suitability of a material for their own process1.
Reliability of the Supplier
The lack of standardization and oversight for the manufacturing of raw materials makes it difficult for biomanufacturers to determine a supplier’s true compliance with GMP standards. Ensuring that raw materials are sourced from reliable and trustworthy suppliers who produce materials of the highest quality in GMP-certified facilities help reduce the burden of qualification on CGT manufacturers.
To be considered GMP-certified, a facility must meet industry-standard quality specifications that assure proper design, monitoring, and control of manufacturing processes and facilities, as well as the systems and processes used for the distribution of the products. GMP certification verifies that products produced in a facility meet the appropriate quality standards, are safe for use, and provide confidence to biomanufacturers who are ultimately responsible for producing consistent, safe, and high-quality CGT products.
Recommended Best Practices for Success
Implement GMP Raw Materials Early On
Because CGTs/ATMPs are subject to strict regulatory requirements, using GMP-grade raw materials early in the development process help ensure the final product will meet these requirements. This can speed up the regulatory approval process and reduce the risk of delays or setbacks associated with having to “qualify up” a research use only (RUO) raw material to meet regulatory requirements down the line4.
By following GMP, raw materials are manufactured under standardized conditions and processes governed by quality oversight to ensure they are produced in a controlled and consistent manner. This can help to reduce batch-to-batch variability and improve the overall consistency of the final product.
Opt for Chemically-Defined Formulations Where Possible
Overall, best practices recommended by regulatory experts is for biomanufacturers to use GMP-grade and animal-derived component-free (ADCF) or chemically-defined (CD) raw materials, procured from safe and traceable sources to achieve the most control and consistency in their process1,3. The most important reason is to ensure the safety of the CGT being manufactured. And secondly, animal-derived components such as fetal bovine serum (FBS) are heterogeneous in nature, which negatively impacts product consistency5.
There is also an industry-wide initiative to transition towards CD raw materials in the CGT supply chain where possible. This allows for better predictability of product performance since CD materials are well-characterized and have a consistent composition, ideal for GMP production.
Closing Remarks
Biomanufacturers of CGTs face a complex developmental and regulatory landscape to bring new products to market, and there are many challenges and chances for failure along the way. Working with a trusted raw material supplier can help address problems early on to ensure consistency and minimize likelihood of failure during the transition to larger scale production for pre-clinical, clinical, or commercial use.
About BioLegend
BioLegend is a leader in the field accelerating research and discovery by providing high-quality GMP recombinant proteins, functional antibodies, and cell culture reagents for use throughout the bioprocessing workflow. BioLegend is ISO 13485:2016 certified, and their GMP facility is ISO 13485:2016 and MDSAP certified. As such, our GMP products come with quality documentation and full traceability, under independent Quality Assurance oversight. Drug master files will be available for many of the GMP products to help manufacturers with regulatory filings.
Footnotes
-
1. Lim SP and Sakina Gooljar S. Challenges in qualification & management of raw materials in advanced therapy medicinal products. Cell & Gene Therapy Insights 2022; 8(2), 269–277 doi: 10.18609/cgti.2022.043
-
2. Campbell A, Brieva T, Raviv L, et al. Concise Review: Process Development Considerations for Cell Therapy. Stem Cells Transl Med. 2015;4(10):1155-1163. doi:10.5966/sctm.2014-0294
-
3. Lebrun AS and Brenner C. Master ATMP processes by controlling raw and starting material. Cell & Gene Therapy Insights 2021; 7(2), 265–271 doi: 10.18609/cgti.2021.034
-
4. Gazaille B, Janssen B and Burger S. Raw Materials for Advanced Therapies: When the Process Is the Product, Ingredients Are Key. BioProcess International. Published June 18, 2021. Accessed February 13, 2023.
-
5. Mack A, Matthews T, St. Germain B, et al. Considerations on impact of raw material variability in gene therapy manufacturing: applying lessons learned from biologics manufacturing. Cell & Gene Therapy Insights 2020; 6(2), 407–414 doi:10.18609/cgti.2020.024