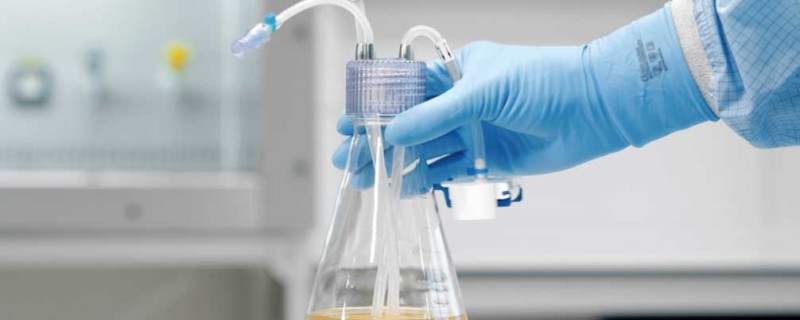
Minimize Cell Culture Contamination and Batch Failure by Creating a Closed System for Cell Culture Expansion
Batch failure due to cell culture contamination is a serious consideration for biomanufacturing. A recent BioPlan Associates Survey examined the frequency, cost and leading causes of batch failure. They found that on average a failure occurs every 9.4 months and costs companies $1 to $2 million. The leading causes of batch failure were contamination and operator error. It is logical that anytime the cell culture system is open, for instance when opening flasks during cell expansion, there is an opportunity for contamination.
Recently, Sartorius launched a new product, MYCAP® CCX Cell Culture Expansion system that addresses the problem caused by opening flasks during cell culture expansion, thereby closing the system and enabling a production process that is less likely to become contaminated.
In this mini-webinar, Charles Meadows, Product Manager for Sartorius MYCAP® CCX Cell Culture Expansion system discusses a new cap that was specifically designed to eliminate the need to open flasks during expansion.
Cell Culture Expansion – Closing the System
Charles began the webinar by explaining how the product was invented and how it streamlines operations, reduces costs and fights batch failure due to contamination. He explained that every cell cultivation begins with a vial of cells from a working cell bank and that these cells must be scaled up to a sufficient population when they can be transferred to a bioreactor. To scale up suspension cultures, the cells are transferred to successively larger Erlenmeyer shake flasks until the desired population is reached.
At each transfer or passage to a new flask, cells are sampled for total count and viability, fresh media is added to the next flask and the culture is transferred to the receiving flask, usually by hand pipetting. The risk of contamination is great during this process because the flasks have to be opened for each of these operations and when the flask is opened there is a risk of compromising the sterility. If a contamination does occur then the expansion process is abandoned and the culture is thrown away wasting precious time and resources.
Cell passaging is typically done in a biosafety cabinet, or laminar flow hood to protect against contaminations. However hoods are large and expensive to operate and to maintain. In addition, every item used in the hood including pipettes, pipette tips, flasks, media containers, even gloved hands needs to be decontaminated first. GMP’s require an environmental monitoring program, which includes settling plates or air sampling plus testing. Most agree that operating outside of the hood would be simpler and less expensive. And still, despite working in a hood, many expansion processes continue to have some rate of contamination. Because of this, backup flasks are often included at many passages. The purpose of a backup is in case a flask becomes contaminated, operators can use one of the backups rather than abandon the expansion which could be days or weeks old. Eliminating backups in an expansion process would save time and reduce costs.
A Novel Cap Design Minimizes Contamination and Streamlines the Expansion Process
To address these issues, Sartorius developed an improved cap for Erlenmeyer flasks, the MYCAP CXX. Most cell lines simply don’t grow well in flasks traditionally vented by disc filters because there is not a large enough volume of air moving across the filter membrane. Using a novel manufacturing design, the MYCAP CXX has holes formed into the cap and components, usually tubing, are inserted into the holes. Then silicone is dispensed into the cap to encase the components and form an elastomeric closure. Charles explains that this manufacturing versatility was the key in integrating our specialized gas exchange cartridge. The cartridge maximizes the opening to the filter membrane and optimizes the footprint allowing us to include integral tubing alongside the gas exchange cartridge. The gas exchange cartridge also has a significantly larger surface area than disc filters and is even larger than the opening on a traditional vented cap. MYCAP CCX combined two technologies into one: the large open surface area of vented caps and the integral tubing of transfer caps.
MYCAP CCX Performance
Charles then presented data showing the performance of MYCAP CCX compared to a traditional system. They conducted parallel expansions on 500mL to 3L flasks starting with the same vial of cells from the working cell bank. They found that double times were nearly identical between the two systems and the statistical T-Test confirmed that there was no statistically significant difference between the growth rates of the two systems.
Because all cell lines are different, Charles shares that Sartorius has built a tool to assist with the design, execution and interpretation of results for a validation study on customer’s cell lines. Customers just have to describe the cell expansion process and the tool will create a materials list and data table. Then just enter the data into the table and the tool automatically generates charts and completes T-Tests.
These outputs can be included with the change control to demonstrate equivalence between MYCAP® CCX and the incumbent system.
MYCAP® CCX Operating Expenses
Charles closes by stating that changing to MYCAP® CCX is a modest and very manageable change with significant upside.
He said that they looked at four categories of operating expenses in a Cell Expansion Operation:
- Cost of Consumables
- Cost of Media
- Cost of Environmental Monitoring
- Cost of Labor
As expected, cost of consumables is higher with MYCAP® CCX. However all other costs are reduced significantly. Overall, they expect MYCAP® CCX to reduce operating costs and models demonstrate a 9% reduction in costs but results may vary. Sartorius will work with customers using proprietary tools to calculate a cost comparison with their specific operations and costs taken into consideration.
In Summary
MYCAP® CCX advances Cell Expansion operations by eliminating the need to perform operations under a laminar flow hood and at the same time reduces the risk of contamination from non-aseptic operations.
MYCAP® CCX is currently available on Corning’s Plastic Erlenmeyer Flasks.
Please visit the Sartorius website to learn more about MYCAP® CCX
About the Presenter
Charles Meadows is Head of Product Management for Sartorius-Stedim Biotech Smart Consumables business and is responsible for MYCAP® Bottle Closures and QUICKSEAL® Aseptic Disconnect. Mr. Meadows came to Sartorius through the 2014 acquisition AllPure Technologies. A founding member, Mr. Meadows was responsible for MYCAP®, QUICKSEAL® and the TAKEONE® aseptic sampling device at AllPure Technologies.
Prior, Mr. Meadows guided the successful acquisition of Mitos Technologies by Parker Hannifin. Mitos manufactured single-use bioprocess equipment including the FreeFlow® valve, DuraPure® process bags and PoGo® single-use mixing system.
Mr. Meadows has a degree in Biological Sciences and holds a Masters in Business Administration with a focus on New Ventures and Entrepreneurial Studies.