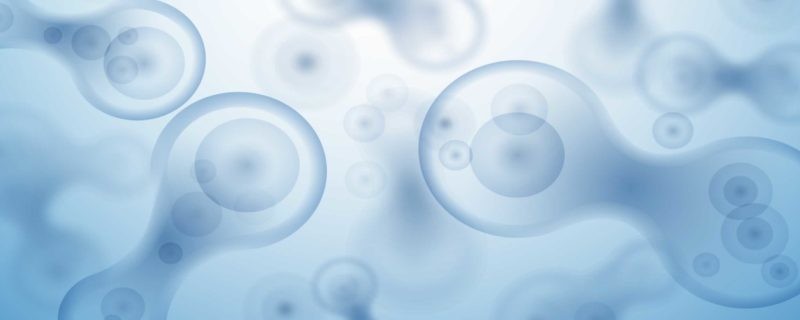
Quality vs. Cost in Biopharmaceutical Manufacturing – Ways to Acheive Both
A major topic of discussion at Biomanufacturing Summit 2012 was the concept of cost versus quality. A striking trend of an increasing number of quality problems and subsequent increase in warning letters has appeared over the last decade in the biopharmaceutical industry. To stay competitive, companies have tended to drift toward a “cost-first” mentality that has been reinforced by the current economic situation in the United States and around the globe. Of course, in the industry of biopharmaceuticals, a mentality that emphasizes cost above quality is doomed to failure. Considering the consequences of failure in manufacturing of a biopharmaceutical, any emphasis of cost at the expense of quality is short-sighted and does a disservice to both the company as well as the patients that the company is meant to serve.
In the long run, quality problems can cost companies far more than just the cost to fix the initial problem. There are also problems with disruption of manufacturing, drug shortages, and competitors capitalizing on these issues to gain more market share. In June 2009, Genzyme discovered a viral contamination in one of its plants that led to a shut down and clean up, which lasted three months. Two of their most successful drugs went into severe shortages – Cerezyme to treat Gaucher Disease and Fabrazyme to treat Fabry Disease. The plant shut down resulted in rationing of the drugs and only the patients most in need received treatment at partial dosing. As a result, Genzyme’s competitor Shire received Food and Drug Administration (FDA) fast track status for their experimental Gaucher Disease treatment in an effort to relieve the shortages with Cerezyme. Shire also picked up significant market share on their drug to treat Fabry Disease, which competed with Fabrazyme. Prior to the Genzyme manufacturing problems, Shire had 45% of the market, this rose to 80%.
In addition to new competition from Shire, a collaborative effort between Protalix and Pfizer introduced a third competitor to Cerezyme and one made using a plant-based biomanufacturing system that promises improvements in cost and quality. Protalix was granted a May 1, 2012 action date under the Prescription Drug User Fee Act (PDUFA). Additionally, Pfizer has filed a Marketing Authorization Application (MAA) to the European Medicines Agency, and Protalix has submitted marketing applications in Israel, Brazil and Australia.
On top of the lost revenue and lost market share from new competition, Genzyme also faced FDA fines. All these problems left Genzyme vulnerable and in February 2011 Sanofi-Aventis announced that they were acquiring the company.
Genzyme’s manufacturing contamination is a good example of why it is critical that quality not be compromised in the production of biopharmaceuticals, but how can a biopharmaceutical company of significant size be sure that quality exists in each step of their supply chain? One way to reduce the threat to quality is to eliminate animal-derived ingredients from manufacturing. Animal-derived ingredients carry a constant risk of contamination from adventitious agents including viruses and prions. While many biopharmaceutical companies using CHO cells for manufacturing have already transitioned into animal-free culture conditions, many have not and animal-derived ingredients are regularly used in manufacturing human vaccines, animal vaccines and stem cell therapies. With cell culture media optimization, animal-derived ingredients can be removed and replaced with recombinant proteins designed to replace key components of serum. When used in combination with appropriate media, these supplements including recombinant albumin, recombinant transferrin, and Animal-free ITSE can provide a safer cell culture system, while maintaining productivity and stringent cost demands.
Another key factor in protecting quality is selecting raw material suppliers that share the same commitment to quality. It does not matter if your manufacturing process is impeccable, if raw materials are not manufactured with the same care, you could be introducing major problems into your manufacturing process.
As an example, at InVitria we designed a completely animal-free and dedicated facility that manufactures Cellastim (recombinant human serum albumin) under cGMP (current good manufacturing practices) in the USA using processing materials that are certified animal component free. InVitria’s adoption of cGMP underscores a commitment to quality that is required in the biopharmaceutical industry. This commitment to quality across the supply chain is an important part of maintaining high quality final products and maintaining patient trust and long term business value.
For Further Reading: