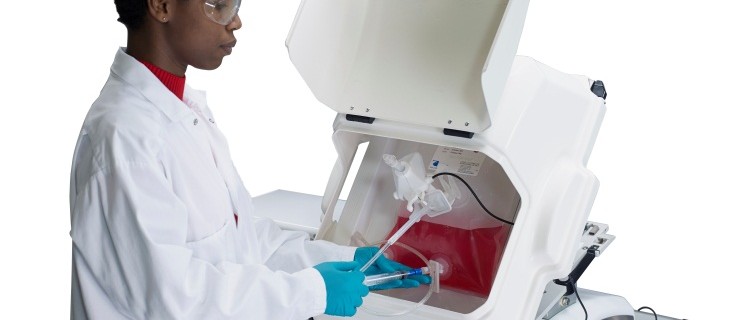
Raising the bar for rocking bioreactors: Introducing the ReadyToProcess WAVE 25 system
A Guest Blog by Cecilia Annerén PhD, Product Manager WAVE Bioreactor Hardware, GE Healthcare Life Sciences
The WAVE Bioreactor™ system was the first single-use bioreactor on the market when it was introduced in the late 1990s. The system, comprising a rocker with a built-in CO2 mixer and a single-use Cellbag™ bioreactor cell culture chamber, was an immediate success. A major reason for the system’s fast uptake was its simplicity and ease of use. Since then, the WAVE bioreactor systems are used in an increasing number of applications such as culturing of Chinese hamster ovary (CHO) cells for monoclonal antibody production, perfusion culturing of T-cells for Cell Therapy, and culturing of Vero cells on microcarriers for vaccine production, to name a few.
With users becoming more diverse, the needs have also evolved. Researchers in academia request versatile, yet simple-to-use, systems that readily generate large amounts of high-quality and publishable data that will help drive science forward. The needs within process development are similar to those in the academia but, in addition, process developers are looking for systems that can offer automation, reduce turnover time, and meet industry guidelines such as the process analytical technology (PAT) initiative. End users in the biopharmaceutical manufacturing space are, in turn, constantly challenged to meet new regulatory standards, while increasing product yield and reducing hands-on time. A simple rocker can still be sufficient for many applications but an increasing number of users are seeking more advanced systems that provide accurate pH and dissolved oxygen (DO) control, perfusion capabilities, CFR Part 11 compliance, and/or that are able to connect to external surveillance and control systems such as DeltaV™.
Some small-scale bioreactor systems are easy to use but might lack vital functions such as pH control, data logging, and report generation. More complex bioreactor systems usually require system tuning and method development performed by skilled personnel to be fully functional and the start-up time can be deterrent.
When GE Healthcare Life Sciences decided to upgrade the existing WAVE Bioreactor system, one of the main goals was to provide advanced measurement and control features and, at the same time, keep the simplicity and inherent ease of use that comes with the rocking bioreactor technology. The recently launched ReadyToProcess WAVE 25 bioreactor system meets these requirements with built-in intelligence and many new features that make the system exceptionally simple to use (Fig 1). To deliver a reliable and robust performance the system has been designed to make hardware, consumables, and control software work together in a true, integrated manner.
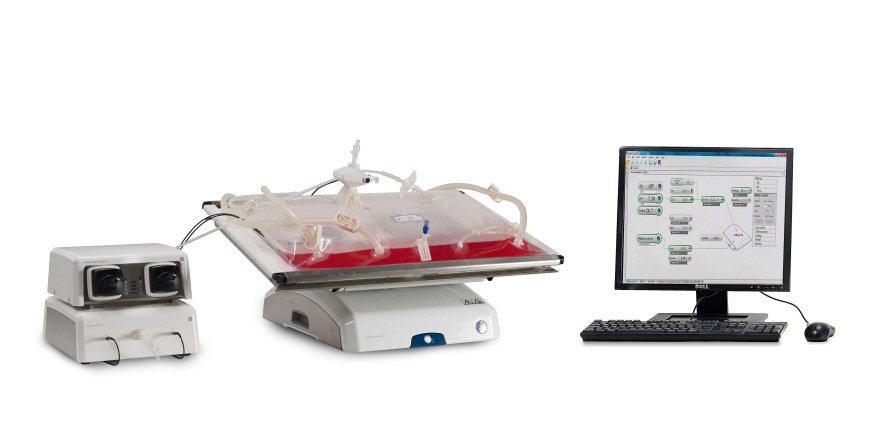
Accurate and intelligent process control
Accurate control of key parameters, such as temperature, pH, and DO, is key to a successful culture performance, and for this to be achieved, the controller must be tuned to find optimal PID parameters for the specific application. This task is not trivial and may require time-consuming, manual adjustments by skilled and experienced users. To facilitate fast start-up and to obtain stable process conditions, the software of ReadyToProcess WAVE 25 includes a library of predetermined and verified control parameters. These parameters are automatically selected by the system based on feedback from sensors and scale in response to the specific application. For example, when pH is controlled using CO2, acid, or base, the user only needs to enter the pump tubing diameter and the acid/base molarity. From this information in combination with feedback from load cells and pH sensors, the software calculates the needed CO2, acid/base flow rate, PID parameters, transition delays, and cycle times during the run, to generate a constant pH with negligible oscillations.
Easy to use
In ReadyToProcess WAVE 25, the software is designed with usability as a key feature. The process picture is easy to interpret, menus are easily accessible, and texts and graphics are intuitive. Other simplifying features include a fast-fill function for quick filling of gas into the Cellbag bioreactor and autocalibration of pump flow rates before and during perfusion culturing. A software Method editor allows programming of a series of instructions that will be automatically executed. This feature can be used for complete automation of cell culture runs, from filling of the bioreactor bag with gas mix or media to final harvest of the culture. Methods can also be employed to automate specific procedures, such as cell culture set-up or addition of daily feeds. The methods can be run in the background while the rest of the procedure is run manually.
Also the hardware has been designed with user friendliness as the main theme. The possibility of tilting the tray in a 50 degree position, for example, simplifies sampling and harvest. The tilt position omits the need for heavy lifting and allows the use of gravity for quick culture recovery (Fig 2). The lid is designed with increased space for tubing and cables. The wide top opening facilitates for the user to interact with the culture without removing the lid.
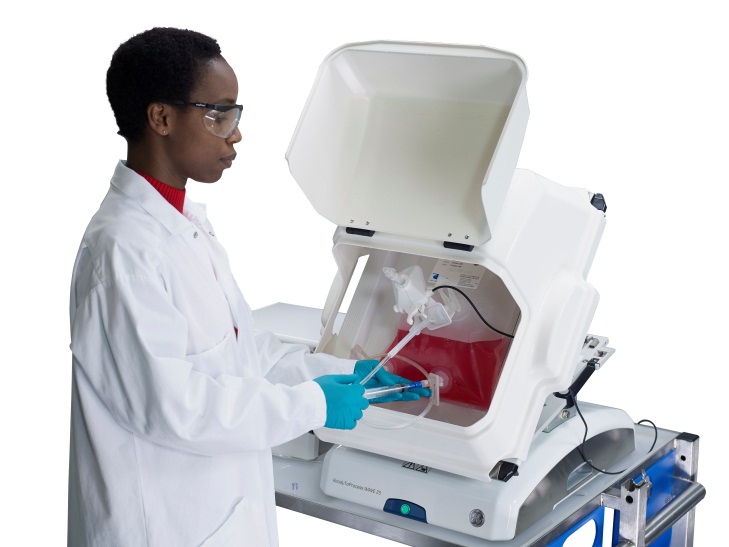
Conclusion
The bioprocessing community is continuously evolving, which is reflected in ever-changing user requirements. The new ReadyToProcess WAVE 25 system was developed with the goal of keeping the simplicity and ease of use of single-use, rocking bioreactor systems, but at the same time enhancing system features with novel, robust, and intelligent technologies. Although different users will have different needs, we believe that many will gain from a system that helps reduce hands-on time, while delivering highly reliable and reproducible results. ReadyToProcess WAVE 25 provides users a peace of mind that allows them to reliably attend to other tasks. More information is available on the ReadyToProcess WAVE 25 product page.
For more information on WAVE Bioreactor Systems, please see:
- “Our Favorite Innovative Uses of the WAVE Bioreactor Technology,” Cell Culture Dish
- “Catch the WAVE – A Review of our Ask the Expert Session on using the WAVE Bioreactor for Research and Manufacturing Operations,” Cell Culture Dish