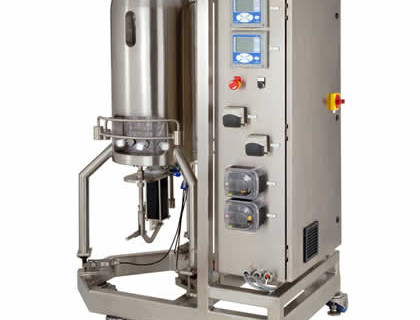
Single-Use Bioreactor Mixing: How to meet familiar requirements with novel technologies
A Guest Blog by:
Ken Clapp, Product Manager Bioreactors, Xcellerex, now part of GE Healthcare Life Sciences
Eva Lindskog, Upstream Marketing Leader, GE Healthcare Life Sciences
Single-use bioreactor mixing: how to meet familiar requirements with novel technologies
A critical feature of a bioreactor system is the technology used for mixing. Different aspects of mixing and mixing technologies have been extensively studied in conventional bioreactor systems made of glass or stainless steel. However, the design proven in conventional systems is not always directly transferrable to a single-use format without modifications. Hence, it is necessary to understand the interrelation between the physical features of a bioreactor system and how these features ultimately affect the performance of the system (Fig 1).
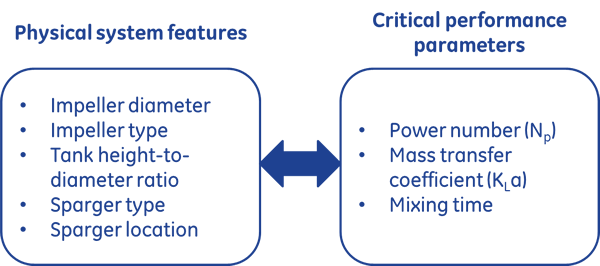
In stirred-tank glass and stainless steel systems, mixing is done with impellers that can be in different configurations. The impeller type, along with the number of impellers and their placement, is application-specific in order to achieve a well-mixed process with adequate mass transfer to support culture growth while balancing impact on organisms or cells. For example, cultures that require powerful mixing, such as microbial fermentation, commonly rely on flat-bladed Rushton-type impellers. This impeller type is excellent at rapid, sustained mixing and gas bubble shear. Mammalian cells, however, are more shear-sensitive, and typically require impellers designed with pitched or curved blades. Cell culture-specific impellers provide axial flow and top-to-bottom mixing with manageable shear. It should be noted, though, that many cell lines now used in industrial biotechnology applications can handle higher shear forces than initially understood [1]. Mixing can also be obtained by gas bubble motion, as in air-lift or bubble-column bioreactor systems, but this technology will not be discussed here.
Requirements for mixing in single-use bioreactor systems
In single-use bioreactor systems, the mixing technology needs to be adaptable to the disposable nature of the operation, while meeting the basic requirements of mixing at a suitable shear level for the specific organism to be cultured. These requirements need to be met without compromising the sterility of the disposable culture chamber. For example, potential risks associated with moving parts in the interface between the impeller shaft and the disposable bioreactor bag, have to be managed. Elimination of such risks can be managed via design features, or by using standard operating procedures.
The mixing device also needs to be inert to avoid contamination of the culture with leachables and/or extractables. Impellers and other in-bag mixing devices are made of molded hard plastic material, for example, high-density polyethylene, whereas the culture bag is made of a soft, flexible film with a contact layer often consisting of low-density polyethylene or ethyl vinyl acetate. Profiles for leachables and extractables from all parts of the bioreactor system, need to be considered in the qualification of the single-use system.
In addition, the mixing device should be easy to handle and mounted inside the bioreactor. At small scale this is usually not a problem. However, the larger the scale, the greater the complexity, in operations as well as in logistics. Single-use bioreactor consumables are commonly purchased when needed, but a stock is required as a back-up. The size of the stock is dependent on, for example, the business need and the delivery time of the consumable. However, bulky mixing devices will require large storage space and add to the complexity of the logistics. In addition, very large mixing devices can be heavy, and misaligned movement during transport and unpacking might disrupt the integrity of the plastic film of the soft-shell, single-use bioreactor, or compromise with the mixing device as such. Therefore, it is recommended to use a mixing device as simple as possible for the specific needs of the application in question.
Examples of mixing technologies in single-use stirred-tank bioreactor systems
There are a variety of mixing technologies and devices for single-use bioreactor systems. Some technologies depend on mixing by using external forces, as in orbital-shaken and rocking bioreactor systems. However, the majority of single-use stirred-tank systems are designed with internal mixing devices. The connection between the mixing device and the motor differs depending on the specific system design but the single-use, stirred-tank bioreactors can be broadly classified as top-driven or bottom-driven.
Top-driven mixing devices are available in a couple of different designs. One ready-to-use solution uses a gamma-irradiated plastic shaft and impellers assembled inside the bioreactor bag. The shaft is attached to a stirrer motor via a magnetic coupling at the top. To meet the power requirement of the process, sufficient magnet strength is needed to handle the viscosity of the process fluid. Another design solution for a top-driven mixer comprises an external stainless steel shaft inserted into a shaft-holder in the disposable bioreactor bag. The end of the shaft couples with a sterile impeller inside the bag. This solution commonly requires ladders for the bag set-up and a ceiling height high enough to accommodate both bioreactor system height and shaft length during the insertion. In the latter case, the stirrer motor is off-set at the top of the bioreactor vessel. A third example of a top-driven mixer is a paddle-based device. In this solution, the stirrer turns in a spoon-like movement driven by a motor located above the bioreactor system.
In bottom-driven mixing solutions, the impeller is seal-less and shaft-less, and the impeller system is integral to the gamma-irradiated bag. The most common bottom-driven impellers have a magnetically coupled driving mechanism, which means that the disposable bag can be designed without rotating, mechanical seals, thereby eliminating the risks associated with leaks. Bottom-driven impellers come in a variety of shapes and formats suitable for various kinds of applications. Conventional mammalian cell culture is typically performed using a pitched-blade impeller (Fig 2A). For large-scale applications requiring greater mixing capacity, the number of blades can be increased, for example, from three to four (Fig 2B), and the impeller location in the vessel optimized for effective mixing and mass transfer.
Microcarrier-based culturing has been successfully performed in single-use bioreactors with conventional, bottom-mounted impellers (Fig 2A). For microcarrier-based cultures, the impeller is slightly elevated, compared with conventional suspension-culture impellers. This design was used for the first vaccine IND where the production vessel was a single-use bioreactor. The IND was filed for a yellow fever vaccine in 2009 and the clinical trials successfully completed and published in 2011 [2].
Another application in which single-use systems with bottom-mounted impellers have successfully been used is microbial fermentation. For microbial fermentation, efficient mixing can be achieved with a flat-bladed Rushton impeller with a second, pitch-blade impeller situated on top (Fig 2C). This combination is bulkier than the simple pitched-blade option for mammalian cultures but has been shown to provide a well-mixed process and efficient gas dispersion. Application examples include fermentation cultures of E.coli (OD130) and Pseudomonas (OD375), as well as cultivation of yeast and other fungi [3].
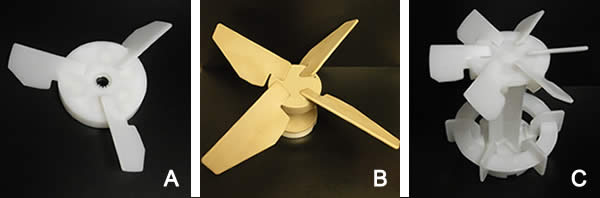
Conclusion
The mixing technology is of crucial importance for efficient, trouble-free, single-use bioreactor operations. There are a variety of mixing technologies on the market: some more suitable for niche applications, whereas others have broader applicability. Proof of principle exists from a variety of processes where single-use bioreactor systems with different impeller technologies have been used, including mammalian suspension cell culture, vaccine production in microcarrier-based cultures of adherent cells, and microbial fermentation.
Learn more
- Cell Culture Dish – “Navigating in the Single-Use Space – How to find the right cell culture bioreactor”
- Cell Culture Dish – “Single-Use Stirred Bioreactors: Enabling Flexible Biomanufacturing
- GE Healthcare Life Sciences Upstream
Footnotes
-
1. Nienow, A.W. Reactor Engineering in Large Scale Animal Cell Culture Cytotechnology. 50, 9–33 (2006)
-
2. Monath et al. An Inactivated Cell-Culture Vaccine against Yellow Fever. N Engl J Med 364, 1326-33 (2011)
-
3. Application note: Microbial fermentation in single-use Xcellerex™ XDR-50 MO fermentor system. GE Healthcare, 29-0564-39, Edition AA (2013)