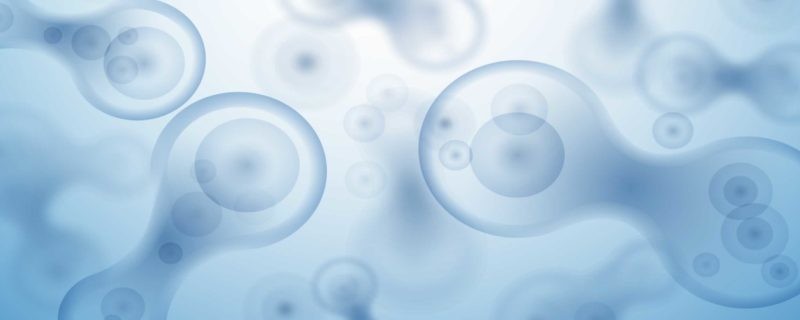
The Impact of the Cell Culture Process on Product Quality
Notes from Cell Culture Engineering Conference (CCE XIII) Apr 22-26, 2012
A guest blog by Steve Pettit, Director of Cell Culture, InVitria
Several presentations at the 2012 CCE XIII demonstrated that the cell culture process has an effect on antibody product quality. Jun Luo (Genentech) showed that proteases released from lysed cells can create C-terminal lysine variants in antibodies expressed from CHO cells. Metal ion concentration in the medium was found to influence the levels of variants with Cu++ increasing the formation of variant, and Zn++ decreasing the formation of variants. This report demonstrates the importance of metal ions on product quality.
Greg Nyberg (Amgen) demonstrated the negative effect of metal ions on the downstream purification of an antibody via ion exchange chromatography. Excess Cu, Fe, and Zn were found to be responsible for inconsistencies in the purification of expressed antibody from CHO Cells. Amgen found that the amount of copper in cell culture medium was ~8x the amount expected in the medium formulation. The source of excess copper was linked to raw materials used in the medium formulation, in particular, the use of ferric ammonium citrate and hydrolysates. Lots of ferric ammonium sulfate were examined and found to contain variable amounts of excess copper. Greg also noted differences in metal vs. plastic bioreactors was most likely linked to the excess. Thus, this report demonstrates that the use of raw materials such as iron chelate compounds and hydrolysates can have impurities that negatively affect product quality
Anne Kantardjieff (Alexion) reported that low cell viability at harvest negatively affects the levels of sialic acid on an antibody produced from CHO cells. The most negative effects were found when antibody was harvested at low, 20-40%, cell viability, a condition that increased the amount of sialases from lysed cells. The negative effect of the sialases was cell line (clone) dependent and was increased by temperature shifts that were used to increase the production of antibody. These results demonstrate the variation between CHO clones expressing a protein product and show that there is an interaction between culture conditions and product quality.
Nathan McKnight (Genentech) found that the formation of acidic and altered glycan antibody variants were associated with media composition and the use of temperature shifts to increase productivity in CHO cells. Cells harvested at higher cell viability had lower levels of variants. Temperature shifts improved cell viability and decreased the level of variants. The type of hydrolysate used also had a modest effect on glycan distribution. Finally, Cu was found to increase titer at the expense of increased deamination of proline. Overall, product quality was improved by reducing copper levels, employing temperature shifts, and by using an alternate hydrolysate source.
Patrick Gammell (Pfizer) noted variability in CHO seed train performance caused by the Lot-to-Lot viability of disposable cell culture bags. Pfizer noted that CHO cells lost viability after the 3rd passage in disposable bags. The problem could be reversed if the bags were washed prior to use. The viability was found in all vendors of disposable bags and was not specific to one vendor or type of bag. The best solution was to screen lots of bags for negative effects on cell growth and to wash bags prior to use.
These presentations show that the quality of raw materials used in cell culture process development and media formulation can cause variability in cell growth, titer, and product quality. Also, the talks illustrate the potential negative effects from the use of iron compounds and hydrolysates.