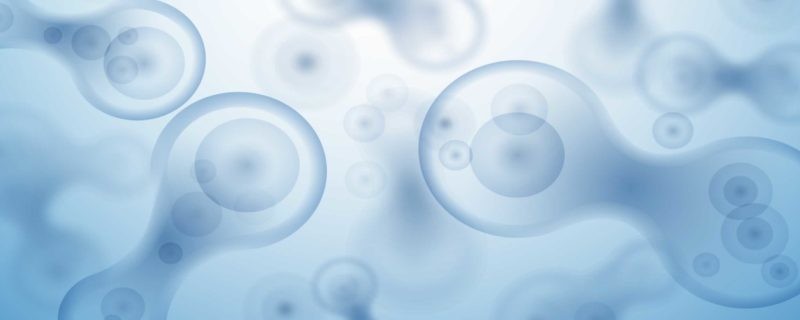
Employing Perfusion Bioreactors to Improve Antibody Production in CHO Cells
In a previous blog “Strategies for Improving Antibody Production in CHO Cells” three areas were identified where antibody production can be improved. In part one of the series titled “Utilizing Gene Synthesis to Improve Antibody Production in CHO Cells,” we looked at gene synthesis as an alternative to classic cloning that offers a precise way to create a gene. In part two of the series titled “Strategies for Enhancing Media to Improve Antibody Production in CHO Cells,” we examined the use of new media supplements to improve cell growth and productivity. In part three we will look at ways perfusion bioreactors can improve antibody production in CHO cell manufacturing.
In the biopharmaceutical industry there is an ongoing discussion about manufacturing capacity vs. demand for biologic drugs. Recently there has been increased concern because several biologic drugs have entered the final phases of the clinical pipeline. If many of these drugs receive approval, capacity could quickly become in short supply. The most common way to increase capacity is to build or expand manufacturing facilities to accommodate more or larger bioreactors. The problem with this approach is that expansion takes a great deal of time and capital upfront before manufacturing can begin. In addition, this approach is not scalable. This means that once the facility is built, it takes money to operate even when no drugs are being manufactured there. If for some reason demand goes down on any of the drugs, companies can find themselves with a lot of costly extra capacity. There is a fine line between not having enough capacity and having too much.
Traditional fed-batch bioreactor systems consist of tanks that are usually between 10,000-25,000 liters. They culture cells in batches that typically run between 7-21 days and product yields are usually 2-6 grams per liter depending on the antibody. In contrast perfusion bioreactors culture cells over much longer periods, even months, by continuously feeding the cells with fresh media and removing spent media. There are two types of perfusion bioreactors. The first keeps the cells in the bioreactor by using capillary fibers or membranes, which the cells bind to. The second does not bind the cells, but rather relies on filtration systems that keep the cells in the bioreactor while allowing the media to be removed.
Perfusion bioreactors offer several advantages over traditional fed-batch bioreactors when addressing problems of scalability and increasing demand. Maybe the most critical advantage is that perfusion bioreactors are smaller in size and can produce the same product yield in less space. Typically perfusion bioreactors operate at 10-30x concentrations compared to fed-batch bioreactors. For example, it has been shown that a 50-liter perfusion bioreactor can produce the same yield as a 1,000-liter fed-batch bioreactor. Alternatively a perfusion system could be used to produce the same yearly yield of antibody in 1/10th the size of bioreactors. Thus, the use of perfusion should enable the replacement of typical 10,000 L bioreactors with 1000L bioreactors without negatively impacting the yearly yield of manufactured product. This size advantage is important because it means that facilities should have the space to add perfusion bioreactors to increase demand as needed rather than having to build new or expand the size of existing manufacturing facilities. They can also turn these systems off if demand goes down with less wasted space than taking large scale bioreactors offline. Similarly, perfusion bioreactors require less on utilities cost and they are less labor intensive to operate. Thus requiring significantly less capital investment on the front end and less on operating costs to manufacture the same yield as fed-batch bioreactors.
Perfusion bioreactors also claim other advantages involving product quality. In perfusion bioreactor manufacturing there is no accumulation of waste products because spent media is being replaced with fresh media continually. Product is also harvested and purified much more quickly, which is particularly helpful if you have a product that is unstable. Lastly, the impact of batch failure due to contamination is also significantly reduced because any contamination involves substantially fewer liters lost. Some proponents have argued that considerable cost savings is a further benefit of perfusion bioreactor manufacturing and this topic was covered in a previous blog titled “Are Perfusion Cell Culture Systems the Future for Cell Culture Based Biomanufacturing,” please read for an explanation of the argument.
Despite stated advantages, the vast majority of biotherapeutics today are manufactured using suspension CHO cells grown in fed-batch culture (typically over a 14-day batch period). There are some biologic drugs manufactured using perfusion bioreactors including Factor VIII from Bayer, ReoPro and Remicade from Centocor, Campath from Sanofi and ReFacto from Pfizer. But overall biopharmaceutical companies have been slow to adopt the use of perfusion bioreactors in large-scale manufacturing. Some critics have expressed concern over the cost associated with the large amounts of media used in a continuous system. However companies that manufacture perfusion systems explain that in large-scale production they should be more cost effective due to a reduction in capital and operating costs.
Perfusion bioreactor manufacturers include GE Wave Biotech, FiberCell, Xcellerex , ZellWerk, ATMI, Refine Technology, AmProtein, and Biovest.
Have any of you used perfusion systems in your production? If so, what were your experiences? Do you think these systems could provide the kind of yield increases necessary to keep up with rising demand?