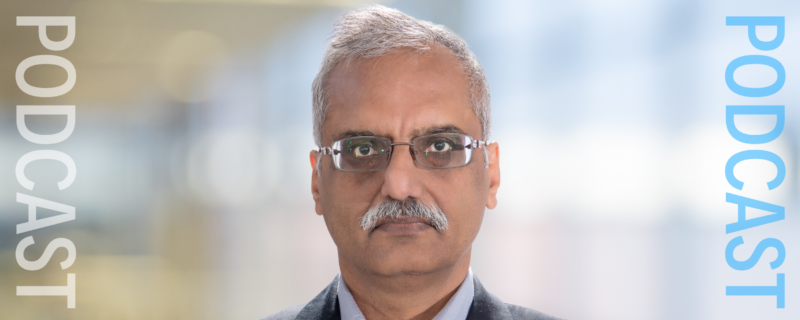
Advancements in Buffer Management and Single Use Inline Buffer Formulation
Podcast: Download (Duration: 15:46 — 12.6MB)
Subscribe Here: Apple Podcasts | Spotify | RSS | More
Subscribe to the Cell Culture Dish Podcast on: iTunes | Google Play
In this podcast, we spoke with Nainesh Shah, Senior Application Engineer at Asahi Kasei Bioprocess about buffer management including the benefits of inline buffer formulation, and single use inline buffer formulation systems.
Buffer Management
We started the podcast by talking about how critical buffer management is to bioprocessing. Mr. Shah discussed how buffers are required in large quantities during the biomanufacturing process and that traditionally buffers were made in large tanks, stored, and used as needed. However, now real estate in the bioprocessing industry is at a premium and companies are looking to utilize new technologies that can reduce facility footprint. For buffer management, it makes sense to create buffer on demand to reduce the footprint dedicated to buffer production in the past.
Inline buffer formulation is a hot topic with companies who require a large quantity of buffer because it provides a way to create buffer on demand in a much smaller footprint. The interesting thing is that it is now also a hot topic among small R&D scale buffer users as well. Inline buffer formulation systems are ideal for users who need 200 to 500 liters of buffer at a time. The system takes the concentrate and adds clean water to provide just the right amount of buffer on demand. Another benefit of inline buffer formulation is that you can achieve a quick process changeover and move on to the next buffer formulation without spending valuable time cleaning the tank, taking samples, and readjusting the critical parameters.
Recently, any new manufacturer, whether it’s a large scale or small scale tends to move into this field of buffer management and operates one or two Inline Buffer Formulation (IBF) systems like the MOTIV™. They then use these systems to make all sorts of buffers needed for their various processes.
The MOTIV Family of Inline Buffer Formulation Systems
Next, I asked Nainesh if he could talk a bit more about the MOTIV family of inline buffer formulation and fluid management systems that Asahi Kasei Bioprocess America (AKBA) offers. He explained how the award-winning MOTIV family has evolved into a series of inline buffer formulation systems designed to help companies move past downstream bottlenecks by driving buffer productivity. The product family includes 3-pump, 5-pump, and custom IBF configurations that can fit most any space, cost, or performance requirements. The MOTIV is a leader in buffer production with a range of scale from 4,500 liters per hour to 10 liters per minute to fit an entire range of volume requirements.
He went on to say that they have added a new feature where MOTIV can fill up bags with buffer and monitor the quantity in the bag to make buffer on demand even easier.
MOTIV SU
Then we talked about the new MOTIV SU, a single use inline buffer formulation system, built to produce complex buffers on-demand effectively and efficiently, all from one pump head, and without the need for CIP/SIP procedures between batches. The innovative design modulates flow through control valves while simultaneously integrating buffer solutions and mixing. As with all the MOTIV systems, OCELOT System Control ensures precise blends every time, controlled by pH and conductivity feedback or flow.
The MOTIV SU is perfect for a biomanufacturer who does not want to spend time with cleaning and validation. It is great for one time use as it does not require time spent in cleaning, validation, and making sure that it is free of all the contaminants and all the buffers which may be harmful for the next process. Another benefit would be if a biomanufacturer used a buffer which had a chemical or ingredient which would be problematic for other processes, and they wanted to eliminate any risk of contamination.
Since the MOTIV SU has replaceable parts, which come as a pre-built unit, it is easy to replace the components and then the system is ready to run again. The MOTIV SU is on the same platform as the MOTIV and is an ideal solution for companies that don’t want to disrupt their regular production lines, but still want to use the same production criteria that in the future could be added to production lines.
Nainesh went on to talk about why single use is such an important option. He said that because there is so much time, energy, and money being spent to clean and provide the proper validation, which then sometimes needs to be reverified or revalidated later. Single use is a good option, and if the process permits, it can be used for a long duration of time provided you have the backup data that you are not contaminating. If you’re using the same material repeatedly, yes, it’s a single use, it’s a replaceable part, but it doesn’t mean that it’s a one time use and then it is gone. It is just like the bioprocess industry using 50 liter and 100 liter bags for holding their buffers, which are all single use and this goes along that same line for the bioprocessing industry.
Single use versus stainless steel
Next he walked through when you would choose a single use option versus a stainless steel option. He explained that a primary consideration would be if you are using anything that would be considered corrosive. If a company is using something in their process and they are not sure whether it is corrosive and they don’t have any documentation or any test reports to show whether it is corrosive or whether stainless steel will hold up and they don’t want to damage the stainless steel equipment, it would be good to have a single use option as a fail proof. They can start bioprocessing studies in the single use system and at the same time start doing some studies with stainless steel to see if there is any issue with corrosion. In six months time, if they don’t find any corrosion issues, they can switch over to a stainless steel option. Another reason to go with single use is color. Any chemist or bioprocessing person would know whether it’s going to impart coloration or affect the stainless steel from the inside, that is again a quick answer to go for a single use option.
Another area where single use is a good option is if you are considering whether to invest and want to prove that your technology works. You could start with the single use and then when you have a more permanent situation you can move into stainless steel.
I followed up by asking if there are any striking differences between the single use and the stainless steel option. He explained that there are a few things that need to be considered when you’re using a single use system. First, because it uses only one pump, which is also a mixer and it creates a suction force to take the concentrates in, there are limitations on the maximum or minimum flow that you can get and the concentrations. It is not good to use very concentrated material and then use a small quantity per minute to do the dilution. So that is a limitation that the user should consider.
The MOTIV SU works on the same principle of mixing feedback control loop for the pH and the conductivity, or the flow and it can control in all the three parameters. It has its own tolerance values that the user can put in of what is acceptable or not acceptable. When it is not acceptable, the system will divert buffer out to a waste outlet and then when it gets back into specification it will revert the buffer back into the product outlet or the designated outlet. Collection of the buffer will start and the system will monitor how much is collected. The user can define and set all these parameters in their method, which are very easy to use and intuitive, just a quick 15-20 minute walk through can get a team up and running.
Set up and operation
Next, I asked if he could talk specifically about the operating system for this unit and also answer the question of if an end user wants to create a new buffer, do they need to come to AKBA. He said that the operating system is based on a Windows based PC housed inside the electrical enclosure with Allen Bradley controls for all the control mechanisms. The user does not have to contact AKBA or work with AKBA if they want to add any new buffer or modify a new buffer. They can make their own buffers, but we teach the user how to make methods via a drop down menu with fill in blanks. Then they can run the method and the system is ready to go. Customers can always come to AKBA if they’re having any issues with making a buffer and we are always there to help guide them through.
Lastly, I asked what the set up is like for end users who are interested in implementing the system. He explained that the regular MOTIV and the MOTIV SU are all skid units which are mounted on wheels that can be easily wheeled in and out of an area as needed. As he said earlier, real estate is very important in the bioprocessing industry and rooms are being utilized for multiple purposes. The mobility of the MOTIV family means that the user can connect to an electrical power supply that can be 110, 220 or 230 volts, in some instances with a higher flow rate it may need the three-phase power supply, but those are all plug ins. Then they connect the air supply for the valves and everything to open. Then connect the concentrate containers, that can be bags, 1 meter cube totes, drums, etc. Lastly, they direct where they want the buffer to go whether it’s going to a container sitting right next to the system, or it could go into a port that can transfer the buffer into another room. That’s it, very easy and no special tools required for starting the system up or shutting it down. The floor size requirement is a typical office table space.
It has a small HMI on top of it to see how the process is moving and all the pertinent data is is displayed there. If there are alarms it will show the user right there what is happening and the operator or the user can take care of it right away
For more information, please download the MOTIV SU brochure.