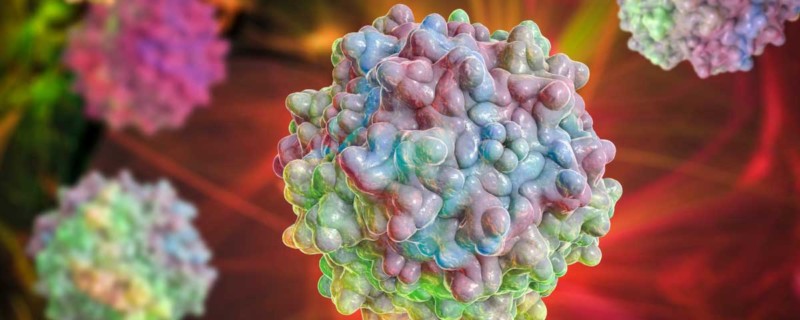
Bioreactor platform supports intensified processes to meet increasing demand for viral vaccines and viral vectors
The industry has been facing increasing capacity demand for virus production due in large part to the success and growing need for viral vaccines and viral vectors. What is the most efficient way to meet these increasing demands in a timely way without building new manufacturing facilities? Univercells Technologies has addressed these challenges by creating a novel biomanufacturing platform that takes advantage of process intensification and scalability to significantly reduce the overall manufacturing footprint and deliver cost-effective manufacturing solutions.
The infographic, Structured cell immobilization – Redefining capacity in biologics manufacture,” highlights how Univercells Technologies is using their innovative scale-X™ bioreactor portfolio to solve the challenges of capacity and scalability in a small physical footprint. The bioreactors, which range in size from R&D to clinical to commercial scale, create a homogenous environment to increase cell density without creating aggregation, all while boosting specific productivity to make each cell deliver more.
Process intensification – Increasing volumetric productivity
The scale-X portfolio of bioreactors offers intensified production for adherent and suspension cell cultures as well as viral products. It has a proprietary structured fixed-bed design that consists of spiral-wound alternating sheets of non-woven PET fabric and spacer netting.
By utilizing a cell immobilization layer and a flow distribution layer, the scale-X line of bioreactors creates an ideal environment to culture healthy cells. By immobilizing the cells, high cell density cultures can be reached, and cells are entrapped which reduces host cell protein release and enables cell retention for continuous product harvest. The flow distribution layer permits the distribution of nutrients in a homogenous, low shear process to maintain the highest level of cell health and productivity.
Scalability – From discovery to commercial manufacturing
The scale-X portfolio covers applications from small-scale R&D to large-scale GMP commercial manufacturing.
- scale-X hydro is designed to support early development
- scale-X carbo is a mid-scale system designed to bridge the gap from development to clinical production
- scale-X nitro provides a solution for large capacity production
To ensure scalability, each system relies on the principle of constant linear velocity of fluids with surface area increases. This means that residence times remain constant for every scale, which enables easy scale up between systems without the need for extensive process development time and cost.
Automated and continuous platform – Supports footprint and cost reductions
The use of automation and continuous production results in a reduction in operational volume, manual operation, overall costs and an increase in throughput.
To learn more about the scale-X bioreactor platform, please download the infographic above.