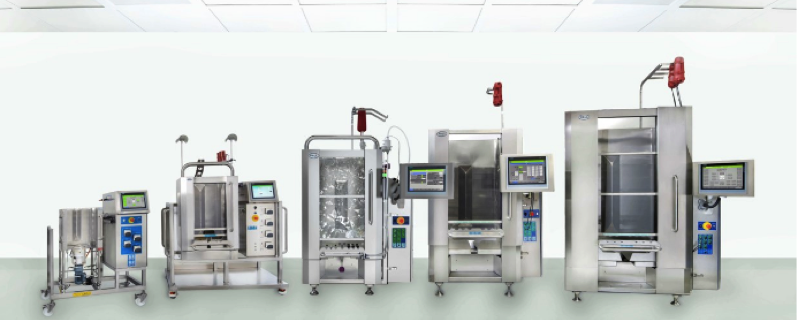
The Addition of Allegro™ STR 500 Enables Seamless Single-Use Bioreactor Scalability from 50 to 2,000 L
Large-scale biomanufacturing frequently relies on single-use bioreactor systems for efficient manufacturing and scale-up. However, one challenge has been predictable scale-up from process scale bioreactors to larger manufacturing volumes. Pall has met this challenge with the Allegro STR bioreactor product line, which includes 50, 200, 1000, 2000 and the new 500 L bioreactor. The consistency in design, engineering and performance across all volumes enables predictable scale-up. In addition, the Allegro STR 500 bioreactor system leverages the usability and process assurance features seen in the entire Allegro STR bioreactor product range.
Allegro STR 500
In keeping with the entire product line, the Allegro STR 500 was designed for thorough mixing using a direct drive agitation mechanism and a large 45° elephant ear bottom-mounted impeller that generates excellent axial and radial flow. The innovative cube shaped biocontainer features baffles that maximize culture homogeneity with no dead zones. In addition, the Allegro STR 500 features a macro ring sparger to deliver gas directly to the culture fluid interface. The unique seating of the macro sparger below the large elephant ear impeller distributes gas delivery directly through the rotating blades of the impeller to maximize mass transfer, as well as facilitating effective CO2 stripping. For more demanding high cell density applications, requiring additional carbon dioxide (CO2 ) stripping capabilities, an optional open pipe sparger is included.
Key features of the Allegro STR 500 bioreactor include:
- Homogenous mixing across the biocontainer can be reached in under 15 seconds in upflow direction.
- Oxygen transfer rates (kL a) as high as 20.5 h-1 can be achieved using 100% air and the ring sparger.
- Stripping of CO2 from the fluid can be achieved using the ring sparger at up to 4 mol.L-1 .d-1 .
- Precise and homogenous temperature control between 37-25 °C ± 0.1 °C.
- Heat up time of 500 L of fluid from 4°C to 37°C can be achieved in under 3 hours when using a Lauda Integral T10000.
- Cool down time from 37 °C to 30 °C is reached in under 1 hour.
Key to Seed Train and Scale-up Operations
Seamless scale-up from process bioreactor to large scale volumes requires careful planning in vessel design engineering, modeling and computational fluid dynamics, as well as actual engineering studies, and live cell culture run performance evaluations. The Allegro STR bioreactor range has been designed to provide predictable scale-up performance, therefore, the comparison of the mixing and mass transfer capabilities across the bioreactor range can be presented from bioreactor to bioreactor at their specified volumes.
Case Study – Scalability Between Allegro STR Bioreactor Sizes in a CHO-S Fed-Batch Process
A case study was performed to demonstrate scalability between the Allegro STR 50 L bioreactor and the Allegro STR 500 L bioreactor. In the study, a CHO-S fed-batch process expressing a recombinant monoclonal antibody, in a chemically defined, animal-derived component-free (ADCF) medium was used. An Allegro STR 50 bioreactor was used as the n-1 bioreactor and seeded the Allegro STR 500 bioreactor at an initial working volume of 385 L. An Allegro STR 50 production bioreactor was then initiated by dropping out 35 L from the Allegro STR 500 bioreactor to ensure comparable culture. The Allegro STR 500 bioreactor engineering parameters were scaled-up from the Allegro STR 50 bioreactor process using a strategy that maintains identical air sparge vvm, air overlay vvm and P/V. Agitation was operated in downflow in both scales.
Comparison of Batch Culture Cell Growth
According to case study data, both cultures grew similarly during their exponential phase and peaked at approximately 26 x 106 cells/mL (Figure 1). After the peak on day 6/7, the VCD in the Allegro STR 50 bioreactor dropped slightly more than the Allegro STR 500 bioreactor. The Allegro STR 50 bioreactor and the Allegro STR 500 bioreactor were harvested at a viable cell density of 23.0 x 106 cells/mL and 24.2 x 106 cells/mL respectively. The cell viability remained > 95% for the first 9 days and were very similar between both scales, the cell viability profile can be found in Figure 2. The first two day’s viabilities are misleading as the Vi-Cell falsely detected dead cells due to a reagent issue, the slightly lower viabilities on days 0-2 should be ignored. The cultures were harvested on day 10 with viabilities at 93.9% in the Allegro STR 50 bioreactor and 94.3% in the Allegro STR 500 bioreactor.
Comparison of Metabolic Data
The metabolic profiles presented show similar trends between the two runs (Figures 2, 3). Slight variations can be observed between the runs, but this can be expected in a cell culture process.
Comparison of Batch Productivity
The productivity between the two scales matched very well (Figures 4, 5). The slightly lower productivity in the Allegro STR 50 bioreactor can likely be attributed to the slightly lower VCD in the latter part of the run and some slight variations in other measured parameters observed in the run.
Conclusion
The study showed similar cell growth, viability and monoclonal antibody productivity across the Allegro STR 50 and 500 L bioreactors when operating at the same power input per unit volume (P/V) and same air sparge and overlay hold up (vvm). When operating under the recommended scaling conditions all metabolic profiles match very well indicating the cell culture is in a similar metabolic state across both scales. Overall, the cell culture performance matched well across both scales and can be successfully scaled up from the Allegro STR 50 to the Allegro STR 500 bioreactor.
For complete study details, please see the application note
Scalability Between the Allegro STR 50 and STR 500 Bioreactors in a CHO-S Fed-Batch Process
For additional information, please see Allegro STR Bioreactor Product Line