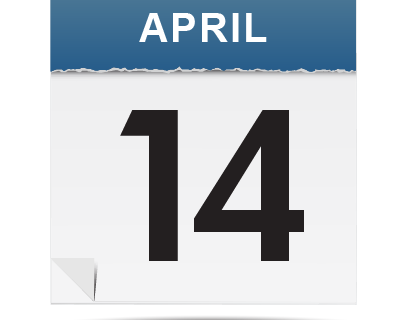
The Dish’s Weekly Biotechnology News Wrap Up – April 14, 2017
This week’s headlines include: FDA continues to approve most drugs faster than its European counterpart, Scotland first UK nation to routinely offer HIV PrEP, GE Healthcare Adds to Its Cell Therapy Portfolio by Acquiring Asymptote, Mesoblast takes off as Cell Therapy for heart failure passes interim test, Roche’s Alecensa notches trial win against Pfizer’s Xalkori, and FDA Delays eCTD Requirements for Master Files.
In Case You Missed It, Recent Articles on Cell Culture Dish and Downstream Column:
GMP Proteins for Cell Therapy Manufacturing: Top 6 Things to Know
Using cells as a therapeutic offers one of the most promising new approaches for treating human disease. These methods include stem cell therapies and regenerative medicine, as well as immune cell therapies for cancers and immune-related disorders. Despite the promise, it has been difficult to bring these therapies mainstream. They are vastly more complex than traditional small molecule treatments or biotherapeutics. For example, in autologous therapies like CAR T, cells are removed from the patient, enriched for the cell of interest, genetically engineered to target the tumor, expanded in cell culture, and re-introduced into the patient as the therapeutic (Figure 1). Many of these steps have yet to be standardized and, along with the inherent variability in biological systems, there is increased potential for unanticipated results and risk to patients…
Smart Cell Culture Monitoring – Transforming the way we look at cells in culture
In this podcast, we interviewed Philip Mathuis, Co-founder and CEO, Ovizio, about cell culture monitoring, the latest technology for monitoring cells in culture without the need for sampling and where monitoring could move in the future…
A Primer on Primary Cells and Culture
Cell-based experiments play a key role in life science, biomedical and pharmaceutical research breakthroughs. The experiments and assays depend on a superior cell culture system and careful selection of cell types. Isolated directly from tissue, primary cells resemble normal physiology and lack modifications associated with immortalized, genetically-altered cell lines. They are first carefully removed and released from tissue, and then established as a growing, healthy cell population in a controlled culture environment. Properly isolated primary cells should be low passage and robust, with high viability, transfection efficiency and doublings. After isolation, the cells can then be expanded, frozen, documented and tested. Researchers can select from many unique human and animal cell types, available in various sizes and packaging configurations, including freshly isolated, cultured, proliferating or cryopreserved cells. Frozen vials, microwell plates, flasks or easy-to-use total kits provide further options. Tissues and cells can also be isolated in matched sets from the same donor…
The Importance of Resin Selection in Development of a Platform Bioprocess Film
Utilizing single-use technologies for biomanufacturing is growing due to several operational benefits including; reduced cleaning and validation, decreased water usage, lower initial capital investment, increased manufacturing flexibility, and faster turnaround time between runs. As the implementation of single-use products has grown, so too has the expectation for improved performance and an increase in the number of application areas involved. Issues have arisen with respect to container integrity, bag flexibility and extractable/leachable profiles. For example, end users want to see single-use products provide the strength needed to maintain container integrity, while at the same time provide the flexibility required for use in applications like bulk liquid transfer and rocking bioreactors. In addition, it is critical that the single-use products do not leach any compounds into the culture that would have a negative impact on the cells or the final product…
Job Outlook for the Biomanufacturing Industry
In this podcast, we interviewed Hillary Kaplan, Director, Bioprocess CMC Development & Operations, Klein Hersh about the job outlook for the biomanufacturing industry from a recruiter’s perspective…
Cool Tool – Scale up with confidence – Introducing ReadyToProcess™ 32 L (450/200)
To reduce costs, increase flexibility and shorten time to market, the use of single use and disposable technologies have increased significantly in biopharmaceutical development and manufacturing. In downstream processing prepacked chromatography columns reduce the need for time consuming cleaning validation and column packing. The last few years has seen a steadily increasing implementation of prepacked chromatography columns in process development and clinical manufacturing. Many of these projects are now scaling up for commercial production…
Fortem: A platform film built for bioprocess
The increase in adoption of single-use bags for manufacturing biopharmaceuticals has been driven by the many advantages it offers. However, the materials of construction can be more complex than conventional stainless steel vessels. Single-use containers are constructed from plastic films, which are often composed of several layers of polymers with additives for processing and performance…
Cool Tool – New KANEKA KanCapA™ 3G for Improved Binding and Milder Elution of Therapeutic Antibodies
Protein A is by far the most common purification method in biopharmaceutical manufacturing. Due to its high affinity and selectivity for therapeutic antibodies, high purity can often be reached in a single step. With the expanding market for therapeutic antibodies, pressure to reduce the cost of pharmaceuticals, and increases in upstream production titers; Protein A improvements have been required to meet industry demands for improved downstream purification efficiency…
Webinars:
Design, Characterization, and Scale-Up Strategy for a New Single-Use Production-Scale Bioreactor – April 27th 11:00 EST
The design of the initial range of single-use stirred bioreactors was cylindrical, essentially copying that of traditional stainless steel bioreactors. The cylindrical shape with dished ends was intended to minimize the expensive steel stainless wall thickness and still be strong enough to withstand the internal pressure developed during steam sterilization. However, since single-use biocontainers can be supplied presterilized, novel shapes can now be considered. Indeed a square cross-section design demonstrates some significant advantages over a cylindrical one.
This GEN webinar will first introduce and discuss the engineering concepts of the Allegro™ STR bioreactors, a square bioreactor design with volumes of 200 L, 1000 L, and 2000 L, and then utilize these concepts to demonstrate scale-up from the bench with a live culture.
Who Should Attend
- Upstream bioprocessing engineers
- Upstream process development scientists
- Clinical and commercial manufacturing supervisors and technicians
- QA/QC scientists
You Will Learn
- Why a square cross-section brings significant advantages to the upstream process, for handling, process assurance, while maintaining optimal cell culture performance
- About the performance of a square-shaped bioreactor, in terms of mixing efficiency, mass transfer of oxygen (kLa), and CO2 stripping
- Applying system engineering principles toward bioreactor characterization, and how tech transfer methods are leveraged across designs, from the bench to production vessels
Cell Culture Events:
World Vaccine Congress – April 10-12, 2017, Washington D.C.
The 17th Annual World Vaccine Congress is the place where the global vaccine industry meets to discuss commercial and scientific issues around regulation, strategy, manufacturing, trials, partnering, influenza, cancer, emerging diseases and veterinary vaccines.
Across 150 sessions, you will learn from leading experts across the issues most impacting on the wider vaccine sector, as well as delve into your specialist area of research and job focus in co-located conferences.
Meet over 700 of your peers in one room and take advantage of the multiple extended networking breaks, co-located World Vaccine Congress (including 7 streams on Immune Profiling, Cancer & Immunotherapy, Influenza & Respiratory, Clinical Trials, Emerging Diseases, Partnerships, Veterinary Vaccines and Bioprocessing & Manufacturing) as well as the evening drinks reception.
For more information, please visit the website https://goo.gl/nJ2bZ1
Cell Culture World Congress USA 2017 – May 24, 2017, Hilton San Diego Resort and Spa, San Diego, CA
The vision of Cell Culture World USA is to provide new, relevant content on process development for cell culture specific scientists working in bio manufacturing companies developing antibodies and immunotherapies. Over 4 years, the Congress has become a technical and networking forum for bioprocessing professionals to provide cutting-edge commentary, present novel and never-before-seen case studies, and highlight technological advancements to the industry.
Our 2017 event will feature a more focused structure, zeroing in on the topics that interest cell-culture specific scientists the most. Immunotherapies are the talk of the industry, and they’ll be a huge topic for this year’s event as well.
Download Brochure: https://goo.gl/t5ZRvx
Register now: https://goo.gl/KTOdxq
Cell Culture & Cell Therapy: Bioprocessing Conference – June 26-27, 2017, Philadelphia
MarketsandMarkets put together a unique platform to establish the reproducible and robust manufacturing processes for the production of stable cell culture and therapeutic cells. At the Cell Culture & Cell Therapy: Bioprocessing Conference scheduled to be held in Philadelphia, USA on 26 – 27 June 2017, leading experts in the industry will be gathered to discuss strategies, technologies and innovations in the area of bioprocessing of cell culture and cell-gene therapies.
Headlines:
“FDA continues to approve most drugs faster than its European counterpart,” STAT News
“Amid ongoing skepticism of the US Food and Drug Administration, a new analysis finds the agency is notably faster at reviewing and approving new medicines than its counterpart in Europe. And the researchers suggest the results, which resemble an earlier comparison, should reassure FDA critics as Congress looks to renew a law that allows the agency to collect industry funds for product reviews…”
“Scotland first UK nation to routinely offer HIV PrEP,” PharmaTimes
“Scotland will become the first UK nation to routinely offer HIV pre-exposure prophylaxis to all eligible patients after the Scottish Medicines Consortium backed the use of Gilead’s Truvada alongside four other new therapies to be funded by the NHS…”
“GE Healthcare Adds to Its Cell Therapy Portfolio by Acquiring Asymptote,” Genetic Engineering News
“GE Healthcare said today it has acquired Asymptote for an undisclosed price in a deal that the buyer said would strengthen its Cell Therapy portfolio with technologies designed to enable the cryopreservation of cellular materials…”
“Mesoblast takes off as Cell Therapy for heart failure passes interim test,” Fierce Biotech
“At the halfway point, a phase 3 trial of Mesoblast’s off-the-shelf Cell Therapy for chronic heart failure is on track and should continue to completion, say advisers. Shares in the Australian biotech hit a 12-month high on the update from the trial, which came after it enrolled 270 out of a planned total of 600 patients with moderate CHF and—crucially—revealed no safety issues with Mesoblast’s MPC-150-IM candidate…”
“Roche’s Alecensa notches trial win against Pfizer’s Xalkori,” Reuters
“Roche’s Alecensa kept people with a specific lung cancer alive longer without their disease progressing than Pfizer’s Xalkori, the Swiss drugmaker said on Monday, as it seeks to move in on the U.S. company’s share of early treatment of the disease…”
“FDA Delays eCTD Requirements for Master Files,” Regulatory Focus
“The US Food and Drug Administration (FDA) is giving drugmakers an additional year before requiring master files to be submitted in electronic common technical document (eCTD) format. In a revised guidance released Friday, FDA says it is delaying the requirement for drug master files (DMF) and biological product files (BPF) to be submitted in eCTD format until 5 May 2018…”