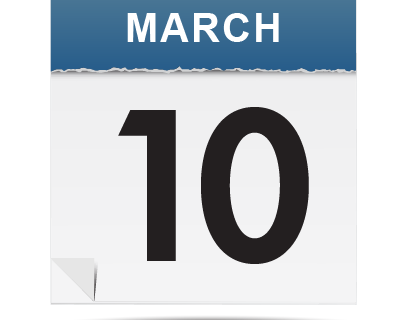
The Dish’s Weekly Biotechnology News Wrap Up – March 10, 2017
This week’s headlines include: Merck and Pfizer’s diabetes therapy under US, EU review, Cancer Pill Gleevec Keeps Patients Alive and Well for a Decade, Exciting Microbe Research? Temper That Giddy Feeling in Your Gut, Sartorius to Buy Essen for $320M to Acquire Live-Cell Imaging Platform, Sanofi, Regeneron say latest Dupixent eczema drug tests positive, and Concert rises after selling CF programs to Vertex.
In Case You Missed It, Recent Articles on Cell Culture Dish and Downstream Column:
We began the podcast with a brief introduction from Fabien Moncaubeig on vaccine and viral vector manufacturing. In this introduction he discussed that the protocols for vaccine and viral vector manufacturing are similar although vaccine manufacturing has a longer history. Both have used adherent cell lines in cell factories or roller bottles. The challenge with these systems is that in order to increase volume you have to scale out rather than scale up. In scaling out you increase the number of pieces of equipment, the overall manufacturing footprint, and the number of employees needed for operation, thus the cost doesn’t decrease significantly…
Mycoplasma contamination is a very real concern for research labs. Mycoplasma contamination can compromise cell culture and experiment results, thus wasting valuable resources conducting experiments that ultimately aren’t accurate. Because mycoplasma contamination actually affects the cells’ overall behavior, contamination can result in false interpretation of experimental results and undermines the validity of the resulting data…
Gene therapies and immunotherapies hold tremendous promise to treat diseases in a completely novel way. As increasing numbers of these therapies move from research and proof of concept to clinical trials, the manufacturing requirements will become more complex. Part of this includes a desire to move away from media that contain animal-derived and undefined components to animal component-free and chemically-defined components. In addition to the possible safety issues, animal components can be variable from lot to lot. Animal components with their naturally occurring cytokines and growth factors can also result in undesired and unexpected effects on cells…
In this mini-webinar, Adam Elhofy, PhD, CSO, Essential Pharmaceuticals, presents data summarizing the findings of a recent study “Novel Cell-Ess ® supplement used as a feed or as an initial boost to CHO serum free media results in a significant increase in protein yield and production” published in Computational and Structural Biology Journal (Volume 14, 2016, p. 319-324) The study focuses on the use of a novel media supplement called Cell-Ess that increases protein productivity via yield per cell while not impacting the metabolic profile via a unique lipid delivery mechanism. Dr. Elhofy initially gave this talk at Boston Biotech Week 2016, and we are excited to be able to share it on the Cell Culture Dish…
Cool Tool – New KANEKA KanCapA™ 3G for Improved Binding and Milder Elution of Therapeutic Antibodies
Protein A is by far the most common purification method in biopharmaceutical manufacturing. Due to its high affinity and selectivity for therapeutic antibodies, high purity can often be reached in a single step. With the expanding market for therapeutic antibodies, pressure to reduce the cost of pharmaceuticals, and increases in upstream production titers; Protein A improvements have been required to meet industry demands for improved downstream purification efficiency…
Continuous Processing Optimization with Smarter Tools
Due to a paradigm shift in the pharmaceutical industry, there is rising pressure to come up with faster, more cost- effective ways to produce drugs for the patients who need them. As orphan drugs and personalized medicine begin to replace traditional blockbuster products, pharmaceutical companies are looking at new and innovative ways to quickly and efficiently deliver drugs to target populations in the thousands rather than the millions. In addition, the need for lower drug prices has been pushed into the spotlight not just by regulators, but also by the advent of biosimilars. As a result of these changes, industry experts must find a way to produce drugs that address the issues around both drug pricing and time to market while also maintaining quality and profits…
Increasing Downstream Bioprocess Efficiency and Overcoming Bottlenecks
In a recent white paper, the issue of improving downstream efficiency was explored. The paper, “Unlocking the Potential for Efficiency in Downstream Bioprocess,” published by GE Healthcare Life Sciences, described techniques like continuous processing, in-line conditioning buffer preparation, and system automation as tools to improve the overall efficiency of downstream processes while at the same time eliminating bottlenecks and facility fit issues. I have summarized the highlights of the paper in this article. Biomanufacturing is constantly evolving due to changing industry demands and new technologies that enable advancement. Industry goals are now primarily focused on reducing cost and improving throughput, productivity, time to market and flexibility. These goals must be met whilst maintaining the highest levels of product quality and safety requirements. With increased titer, downstream processes have had to manage higher titers and greater impurities than they were originally designed for. Thus downstream processes must also be improved to create an entire manufacturing process that is more streamlined and meets industry goals…
The use of Protein A affinity chromatography is commonplace in biopharmaceutical manufacturing, with 95% of all commercially available MAbs using Protein A purification. High purity is achieved in one step (around 99%), but it is well recognized that the cost of Protein A resins is substantial. If a product makes it to marketing approval and manufacturing these costs are amortized over a large number of purification cycles and the contribution to cost of goods is acceptable. However, a high percentage of clinical projects will fail, resulting in the Protein A resin only being used for a small number of cycles – significantly reducing cost-efficiencies…
Upcoming Ask the Expert Session:
Maximizing Transient Protein Production
Companies are turning to transient production of proteins to accelerate timelines, gain quick access to protein for early go-no go decisions, delay stable cell line generation, and reduce costs. Expanding the role of transient protein production within the biotherapeutic discovery and development workflow is highly dependent on the ability to supply the required quantities of quality proteins — generally ranging from milligram to multiple grams of protein — in the required timeframes. Thus, increasing productivity and process scalability are aspects of production that must be addressed.
There are a wide variety of factors that influence productivity – – from pre-transfection factors such as cell type, vector design, and cell health to post-transfection factors such as seed densities, media additives, and feed schedules. In addition, researchers must consider the method of transfection which affects both productivity (cell health & transfection efficiency) and process scalability.
Recently, Cell Culture Dish has published several poster and webinar articles discussing the use of MaxCyte’s electroporation-based delivery platform for cell engineering, specifically in the areas of transient and stable protein production. There was a high level of interest from readers regarding CHO-based, gram-level protein production, and so during this week’s Ask the Expert session, we will be joined by Dr. Weili Wang, the Director of Cell Culture at MaxCyte, to answer questions regarding cell engineering and culturing that can maximize transient protein production. Dr. Wang has over 20 years of biopharma industry experience focusing on process development, stable cell line generation, tech transfer and scale up/scale down modeling to support cGMP manufacturing. Prior to joining MaxCyte, Dr. Wang was the upstream manager at Human Genome Sciences, MacroGenics and Amplimmune. Dr. Wang received his Ph. D degree from Texas A&M University, a Master degree from Florida International University and Bachelor degree from East China University of Science & Technology.
Ask your questions starting Monday!
Cell Culture Events:
World Vaccine Congress – April 10-12, 2017, Washington D.C.
The 17th Annual World Vaccine Congress is the place where the global vaccine industry meets to discuss commercial and scientific issues around regulation, strategy, manufacturing, trials, partnering, influenza, cancer, emerging diseases and veterinary vaccines.
Across 150 sessions, you will learn from leading experts across the issues most impacting on the wider vaccine sector, as well as delve into your specialist area of research and job focus in co-located conferences.
Meet over 700 of your peers in one room and take advantage of the multiple extended networking breaks, co-located World Vaccine Congress (including 7 streams on Immune Profiling, Cancer & Immunotherapy, Influenza & Respiratory, Clinical Trials, Emerging Diseases, Partnerships, Veterinary Vaccines and Bioprocessing & Manufacturing) as well as the evening drinks reception.
For more information, please visit the website https://goo.gl/nJ2bZ1
Cell Culture World Congress USA 2017 – May 24, 2017, Hilton San Diego Resort and Spa, San Diego, CA
The vision of Cell Culture World USA is to provide new, relevant content on process development for cell culture specific scientists working in bio manufacturing companies developing antibodies and immunotherapies. Over 4 years, the Congress has become a technical and networking forum for bioprocessing professionals to provide cutting-edge commentary, present novel and never-before-seen case studies, and highlight technological advancements to the industry.
Our 2017 event will feature a more focused structure, zeroing in on the topics that interest cell-culture specific scientists the most. Immunotherapies are the talk of the industry, and they’ll be a huge topic for this year’s event as well.
Download Brochure: https://goo.gl/t5ZRvx
Register now: https://goo.gl/KTOdxq
Cell Culture & Cell Therapy: Bioprocessing Conference – June 26-27, 2017, Philadelphia
MarketsandMarkets put together a unique platform to establish the reproducible and robust manufacturing processes for the production of stable cell culture and therapeutic cells. At the Cell Culture & Cell Therapy: Bioprocessing Conference scheduled to be held in Philadelphia, USA on 26 – 27 June 2017, leading experts in the industry will be gathered to discuss strategies, technologies and innovations in the area of bioprocessing of cell culture and cell-gene therapies.
Webinars:
Accelerating the development of regenerative therapies: Large scale expansion of human mesenchymal stem cells – March 28, 2017
Pall has partnered with RoosterBio to commercialize Allegro™ Unison human mesenchymal stem cells (hMSCs) and bioprocess media to accelerate Cell Therapy and regenerative medicine development. Use of Allegro Unison products along with SoloHill microcarriers, Allegro biocontainers, and the PadReactor® bioreactor system moves the industry towards execution of the technology roadmap to achieve lot sizes of 100s of billions to >1 trillion hMSCs, without the need for extensive and costly process development. Large scale hMSC expansion is now rapidly achievable in a robust, scalable, reproducible, and economic manner.
This webinar details the total solution for large scale expansion of human mesenchymal stem cells. We will present a case study highlighting large scale cell culture and expansion of hMSCs to billions of cells, within ten days of culture, in a fed-batch 50L bioreactor system.
Register to Learn:
- How Allegro Unison hMSCs and bioprocess media, SoloHill microcarriers and Pall PadReactor systems enable large-scale hMSC expansion.
- Culture protocol for 200-fold hMSC expansion, within 10 days, in a single-use, fed-batch scalable manufacturing platform.
- How regenerative medicine and Cell Therapy developers can rapidly and economically move towards producing tens of billions to >1 trillion high quality hMSCs for product development programs in single-use bioreactors.
Headlines:
“Merck and Pfizer’s diabetes therapy under US, EU review,” PharmaTimes
“Regulators on both sides of the Atlantic are reviewing three new submissions for medicines containing ertugliflozin, an investigational SGLT2 inhibitor being developed by Merck and Pfizer to help improve glycaemic control in adults with type II diabetes…”
“Cancer Pill Gleevec Keeps Patients Alive and Well for a Decade,” NBC News
“Everyone hopes and wishes for that last-minute cancer breakthrough that will save doomed patients. It almost never actually happens. With Gleevec, it did. The once-a-day pill turned chronic myelogenous leukemia, or CML, from a certain death sentence into a manageable disease. Now data shows it’s helped 83 percent of patients live 10 years or longer, even with side-effects that include a characteristic rash, nausea and fatigue…”
“Exciting Microbe Research? Temper That Giddy Feeling in Your Gut,” The New York Times
“While we have long known about the existence of microbes — the tiny bacteria, fungi and archaea that live all around, on and in us — our full relationship has become one of the hottest topics for research only in recent years…”
“Sartorius to Buy Essen for $320M to Acquire Live-Cell Imaging Platform,” Genetic Engineering News
“Sartorius has agreed buy cell-based assay and instrumentation firm Essen BioScience from its private equity owner SFW Capital Partners for $320 million cash. Essen develops instruments, software, and reagents for live-cell imaging and data analysis. The firm’s flagship IncuCyte® platform for real-time, quantitative live-cell imaging and analysis was launched in 2006…”
“Sanofi, Regeneron say latest Dupixent eczema drug tests positive,” Reuters
“Drugmakers Sanofi and Regeneron said on Saturday results from a one-year test of their Dupixent product aimed at adults with eczema or moderate-to-severe atopic dermatitis (AD) had been positive…”
“Concert rises after selling CF programs to Vertex,” BioCentury
“Concert Pharmaceuticals Inc. (NASDAQ:CNCE) jumped $5.99 (62%) to $15.64 on Monday after it said Vertex Pharmaceuticals Inc. (NASDAQ:VRTX) will acquire all of its cystic fibrosis programs, including CTP-656, a deuterated version of Vertex’s Kalydeco ivacaftor. Concert is to receive $160 million in upfront cash and is eligible for $90 million in regulatory milestones…”