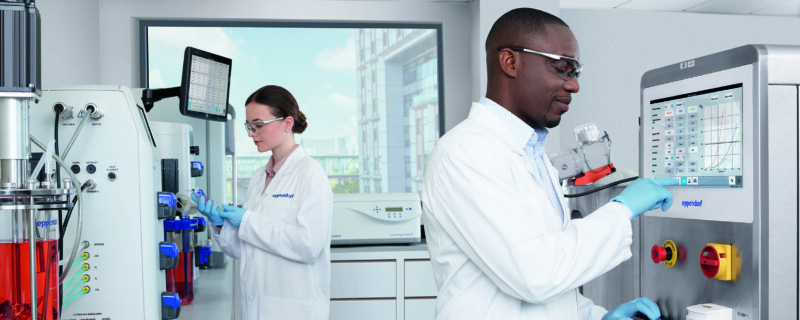
How Stirred Tank Bioreactors and Bioprocess Controllers can Enable Efficient Automation and Scale-Up to Streamline Bioprocess Optimization
For decades, the biopharmaceutical industry has relied on mammalian cells, particularly Chinese Hamster Ovary (CHO) cells, to produce therapeutic proteins, which requires the establishment of robust and scalable manufacturing processes. Development typically starts in the R&D stage where work is focused on identifying and optimizing production conditions using small-scale cultures in shake flasks, cell culture dishes, and T-flasks. This is an economical strategy to evaluate the effects of different variables, such as media composition, temperature, and pH, on the growth and productivity of the cells. The goal is ultimately to transfer these R&D processes to large-scale industrial production volumes to achieve consistently high yields.
An effective scale-up strategy is required during process development to translate small-scale findings into a robust and scalable process to ensure both the reproducibility of cell culture growth and yields at large working volumes— ideally with little or no additional optimization, yet this is often not as straightforward as one would expect. Stirred-tank bioreactors are the most common type of bioreactors implemented during scale-up because their well-understood design principles provide simplified scalability and enhanced reproducibility. Bioreactors equipped with bioprocess control systems offer improved process control and opportunities to incorporate workflow automation to create robust manufacturing processes.
Single-use Bioreactor Systems Enhance Bioprocess Consistency and Streamline Scale-Up
Single-use stirred tank bioreactors have become established in modern biopharmaceutical processes in recent years, directly linked to their unique ability to enhance flexibility, improve turn-around time, and reduce overall costs. Eppendorf’s range of BioBLU® c Single-Use Bioreactors combines all the advantages of single-use technology with the trusted performance and scalability of a stirred-tank design suitable for batch, fed-batch, and perfusion bioprocesses from 100 mL to 40 L. From small scale to pilot scale, the vessels are geometrically and proportionally similar for ease of scalability.
The BioBLU bioreactors are equipped with a pitched-blade impeller and built-in sensor technology to measure critical culture parameters like dissolved oxygen (DO), temperature, and optical measurement of pH to minimize contamination risks from sampling. The integrated sensors transmit information to the bioprocess control systems, which can regulate the action of actuators, like pumps, tempering devices, and gassing devices to automatically adjust and maintain critical parameters at the desired setpoint. These automated feedback loops help increase the reproducibility of culture growth, product formation, product characteristics, and more.
Many strategies using stirred tank bioreactors to streamline the scale-up of bioprocesses such, as constant impeller power per unit volume (P/V), constant tip speed, matching oxygen volumetric mass transfer coefficients (KLa) can be effectively implemented using the BioBLU bioreactors.
Bioprocess Control Systems Enable Automated Process Control
Intelligent bioprocess control stations are widely used in bioprocessing to improve process control, data management, optimization, and to enable successful scale-up from small-scale to large-scale production. The bioprocess control system’s software features enable the implementation of workflow automation to save time and simplify repetitive tasks. Automated control of key process parameters, such as temperature, pH, dissolved oxygen levels, and nutrient feeding rates can minimize process variability. Information from the bioreactor sensors is transmitted to the bioprocess control software, which regulates the addition of CO2 and liquid pH agents, the activity of tempering devices, agitation, and the gassing with air and/or O2 to maintain optimal culture conditions to achieve high cell viability and yield.
By using the same software and protocols across different bioreactor sizes, researchers and process developers ensure that the process is consistent and reproducible across different scales. Eppendorf’s bioreactor control platforms, such as the BioFlo bioprocess control systems, support one of the widest ranges of single-use solutions, allowing the scale-up of your process to up to 2,000 L. The bioprocess control systems offer a range of features for process control, including real-time monitoring and automated control of process parameters, data logging, and remote access capabilities. The user-friendly interface across all BioFlo control systems and improved software allows for easy programming and consistent operation of the bioreactor.
BioFlo® 320 Bioprocess Control System
The BioFlo® 320 bioprocess control system is suitable for bench-scale bioreactor vessels ranging from 400 mL to 40 L and is equipped with universal connections for a wide variety of analog or digital Mettler Toledo® ISM® sensors, including dissolved oxygen (DO) and carbon dioxide (CO2), pH and redox. Additionally, the BioFlo software has been enriched with a variety of new features, such as the Auto Calibration and Scale Up Assist functions, to automate the workflow, saving time, and simplifying repetitive tasks, such as the Auto Calibration and Scale Up Assist functions.
In this application note, Eppendorf experts describe CHO cell culture bioprocesses in batch, fed-batch, and perfusion mode in the BioBLU bioreactors. The BioFlo 320 controller was calibrated using the Auto Calibration algorithm and then used to establish automated glucose feeding and to control pH and DO levels at setpoint.
BioFlo® 720 Bioprocess Control System
The BioFlo® 720 provides a perfect connection between R&D and pilot/production scales since processes developed using the BioFlo 320 can be seamlessly transitioned to 50 L – 2,000 L on the BioFlo 720 bioprocess controller. Developed for manufacturing with FDA-validated processes, the BioFlo 720 can be used in production environments for pharmaceutical products that follow cGMP or 21 CFR Part 11 guidelines (with BioCommand® Batch Control Plus software package). To ensure maximum flexibility and scalability, the BioFlo 720 bioreactor controller is compatible with the Thermo Scientific™ HyPerforma™ 5:1 Single-Use Bioreactors (SUBs). The innovative Auto Inflate function automatically controls the inflation process for flexible SUBs.
Whether the desired scale-up strategy is based on constant P/V or constant tip speed, the Scale Up Assist software algorithm can automatically calculate all critical parameters needed, including gas flow rates and agitation with vessel specific data. This application note shows a real-world example of how the Scale Up Assist feature on the BioFlo 720 was used to successfully scale up a CHO cell culture using the built-in constant power software algorithm.
The combination of scalable single-use stirred tank bioreactor solutions and flexible bioprocess controller systems are purpose-built solutions to streamline tech transfer and implement workflow automation for modern day biopharmaceutical development and production of antibodies, vaccines, and other therapeutic treatments. These systems will be critical to optimize bioprocessing in the years to come to increase productivity, output and drive new innovations in biopharmaceutical production.
For more information, please see https://eppendorf.group/91hyld