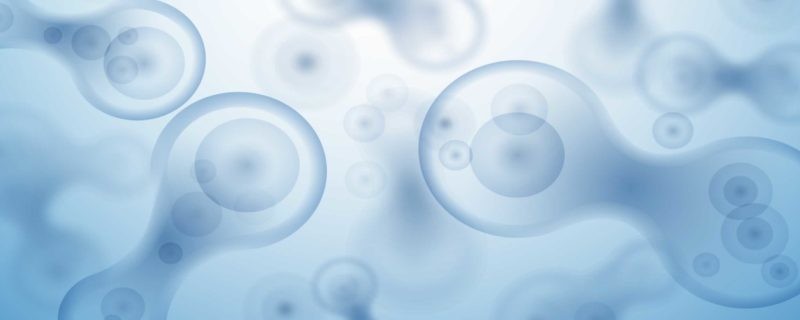
Improving Media to Increase Virus Yield in Vaccine Production
In Part I of our series on “Strategies for Improving Viral Yield in Vaccine Manufacturing,” we will look at ways to improve media to increase virus yield and quality. Cell culture based vaccine manufacturing is centered on growing virus in host cells instead of eggs for example. Viral yield is critical in cell culture based vaccine manufacturing because higher yield results in more vaccine produced quicker. During times of seasonal flu pandemics, this translates into more vaccine being available sooner, protecting more of the public. Also, viral yield leads to lower cost of production because yield is the most important cost driver in vaccine manufacturing. Lower costs can mean the vaccine can be supplied to more people who need it, primarily those in the developing world where the threshold for medical expense is very low. As a result the cell culture community is routinely examining new ways to increase virus yield and quality in manufacturing.
Optimizing media for vaccine production ideally results in a robust, customizable media that maximizes output per cell and enables earlier harvest times. Another key factor is the removal of animal products and a move towards a more defined medium both of which would improve the overall quality and safety profile for vaccine production. Usually vaccine production media contains fetal bovine serum (FBS), but there are problems with this kind of production, including FBS lot-to-lot variability and inconsistency. FBS and animal products in general are plagued by inconsistent product lots, mainly due to the fact that the source material (cows themselves) can be so different based on where they live, what they eat, etc. Some lots of FBS may contain little contamination, others significantly more and some lots may be higher in various nutrient or vitamin components. All of these inconsistencies have a major impact on cells, which makes manufacturing difficult because yield isn’t consistent.
In addition to production problems, the use of animal products raises many safety issues around possible contamination. The Food and Drug Administration (FDA) and other regulatory bodies discourage use of these animal components because of safety concerns involving the risk of viral and prion (the infectious causative agent associated with Mad Cow Disease) contamination. These issues were the impetus, which led biopharma to remove FBS from CHO manufacturing. While CHO manufacturing has made continual improvements over the years, including advances in media formulations to remove FBS; vaccine manufacturing has maintained many of the same practices including the use of animal products in media. The primary difficulty is that manufacturing practices developed for many current vaccines were developed decades ago, before serum-free technology had become a robust approach to medium development. Vero, MDCK, and human dipoid lines (MRC-5, Wi-38), commonly used in vaccine manufacturing, were not able to be easily grown without FBS and as a result cell health and productivity often suffered when serum was removed.
Today the majority of current serum-free media used in vaccine manufacturing utilizes plant-based hydrolysates to enable the growth of cells without serum. For example, the commercial media VP-SFM (Invitrogen), OptiPro (Invitrogen), SFM4MegaVir (Thermofisher-Hyclone) and ProVero (Lonza) include hydrolysates in their formulation. Hydrolysates are notoriously inconsistent, and their use does not solve many of the consistency problems inherent from the use of FBS. Furthermore, the use of hydrolysates can cause inconsistency in cell attachment to microcarriers [1].
The legacy of these cell culture challenges is that most approved viral vaccines still use FBS in manufacturing including the MMR, Polio, Hepatitis A, Rotavirus, and Varicella vaccines. It can be difficult to change the manufacturing process of already approved vaccines due to FDA requirements and the possibility of additional safety or clinical studies. However, vaccines in development would benefit from incorporating a new class of media supplements that are animal-free and defined and allow for the reduction or removal of FBS from virus cultures. These supplements provide a way to maintain the health and productivity of cells without compromising safety. In addition many of these supplements are recombinant and provide the consistency that is lacking in animal products. This improvement in consistency can result in more efficient manufacturing and ultimately lower costs. Two of the recombinant supplements, recombinant albumin and recombinant transferrin, have been successfully used to improve cell viability and yield of cells used for animal-free biomanufacturing. Please see table below for a list of media supplements for vaccine production.
The advantage of these new products is that they eliminate the problems associated with serum, like inconsistency, possible contamination and sourcing challenges, without compromising cell health and productivity, common with serum-free media. They also aid in the transition from serum containing to serum free culture conditions.
Has anyone used any of these products, if so, which ones and how did they work for you?
Type | Product | Cost Per Liter of Media | Source |
---|---|---|---|
Recombinant Albumin | InVitria Cellastim | $1-6 | Animal-free |
Sigma recombinant albumin | Animal-free | ||
Fisher Scientific recombinant albumin | Animal-free | ||
Sheffiled Bioscience rAlbumin ACF | Animal-free | ||
Mediatech cellgro rhAlbumin | Animal-free | ||
Recombinant Transferrin | InVitria Optiferrin | $0.25-$1 | Animal-free |
Sigma recombinant transferrin | Animal-free | ||
Fisher Scientific recombinant transferrin | Animal-free | ||
Insulin-Transferrin Supplements | InVitria ITSE AF | $10-12 | Animal-free |
Mediatech ITS | $15-20 | Animal Derived | |
Life Tech ITS-A | $20-25 | Animal Derived | |
Life Tech ITS-G | $20-25 | Animal Derived | |
Life Tech ITS-X | $20-25 | Animal Derived | |
Gemini BIO ITS | $20-25 | Animal Derived | |
Sigma ITS | $12-15 | Animal Derived | |
ThermoFisher ITS | $12-15 | Animal Derived | |
BD ITS + | $15-20 | Animal Derived | |
Sciencell ITS | $15-20 | Animal Derived | |
Serum Replacement | MP Biomedicals TCH | $150-200 | Animal-free |
Plant-Based Hydrolysates | Sheffield Bioscience Catalog List | $1-3 | Animal-free |
BD Bioscience Catalog List | Animal-free |
Footnotes
-
1. Genzel, Y., M. Fischer, and U. Reichl, Serum-free influenza virus production avoiding washing steps and medium exchange in large-scale microcarrier culture. 2006. (16472544) Vaccine. 24 (16): p. 3261-72.