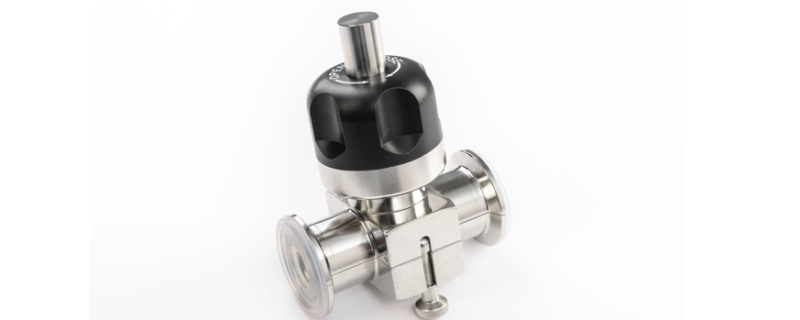
Novel single-use valve design increases efficiency and decreases risk of contamination
There are many challenges facing biopharmaceutical companies during commercial manufacturing. These challenges drive continual improvements in both manufacturing strategy and the associated tools or technologies used. For instance, pricing pressure has increased the need to reduce manufacturing costs. In addition, there has been an increasing desire to produce more products at smaller volumes and create flexible multi-product facilities. Traditional turnaround time, cleaning, sterilization, validation and associated risk of contamination and cross-contamination can create manufacturing challenges in these facilities.
Risk of contamination and cross-contamination have always been and continue to be big concerns. A recent application note, “Rationale Design of Valves for Flexible Processing” discusses an area of contamination risk that has not seen significant improvements – soft parts, specifically diaphragm valves. The application note states “according to an industry survey, soft parts (valve diaphragms, o-rings, gaskets) are the number one process equipment contamination risk which can lead to batch contamination or loss. On top of that the change out of soft parts represents 50% of overall maintenance time underlining the need for solutions in this domain.” Authors went on to describe the current challenges with traditional diaphragm valves and present a single-use direct replacement alternative that increases efficiency and reduces contamination risk.
Problem with Traditional Diaphragm Valves
The use of diaphragm valves for fluid control is common in stainless steel biomanufacturing facilities and has a long history of use. They are also linked to contamination risk and significant installation and maintenance time. In the “life cycle of a traditional diaphragm valve” figure below, authors demonstrate the complex life cycle of these valves due to the consistent use and reuse, they require robust maintenance procedures to ensure components remain fully functional throughout their lifespan (Figure 1).
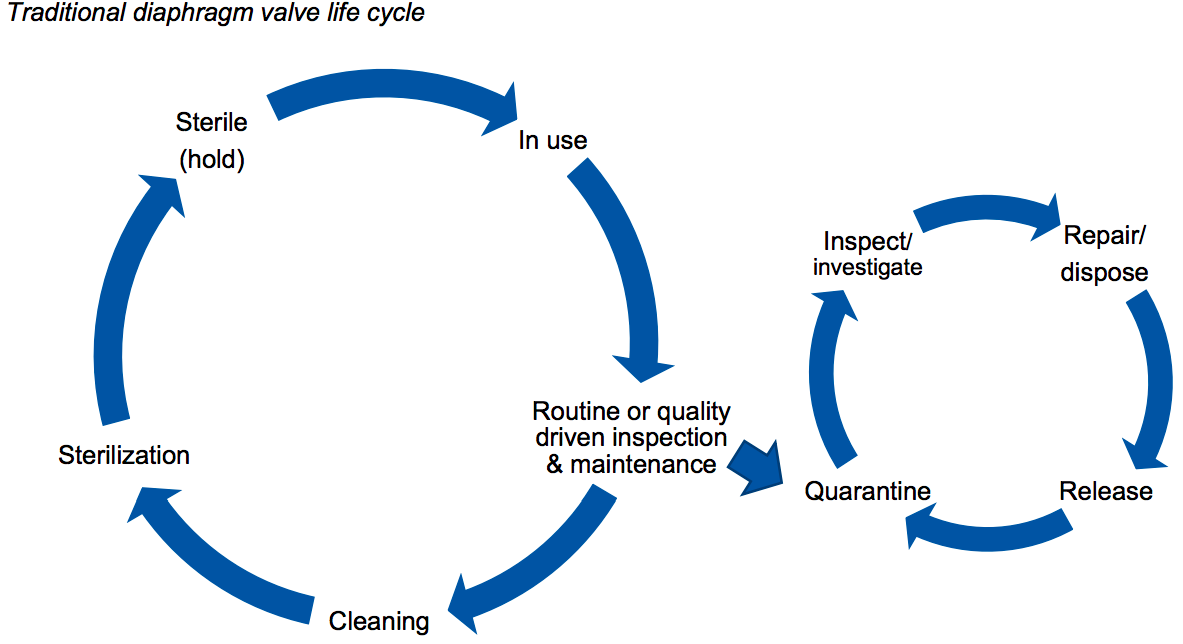
The main drawbacks of traditional diaphragm valves include installation complexity, variable life expectancy, cross-contamination potential, and detrimental flow characteristics. While there have been many design updates to extend required preventative maintenance and reduce operating costs, none have completely resolved the challenges.
Designing a Better Valve
Single-use manufacturing solutions have been known to reduce changeover times, reduce the risk of contamination and cut cleaning, validation and maintenance time. In this application note, Pall Biotech and ARTeSYN Biosolutions present the ARTeSYN Diaphragm Replacement Valve (DRV), designed to replace traditional diaphragm valves. The DRV offers a quick and reliable changeover of its single flow path within traditional piping by creating a product contact flow that is single-use, while the enveloping non-product contact valve hardware is reusable. This unique design removes installation complexity, the need for cleaning between batches, and offers further process efficiency benefits by eliminating shear, cavitation and hold-up concerns.
Comparison Study
Authors present a very interesting study that compares two types of valves – a traditional diaphragm valve with weir and a full bore DRV. In the study they looked at shear strain and pressure drop of both valve types. Results showed that there was a significant shear strain difference with higher shear rates found in the traditional diaphragm valve. Higher shear rates have been shown to have a detrimental impact on drug yield especially in tangential flow filtration applications. Results of the pressure drop study showed that there was a roughly 8-fold improvement in the pressure drop seen in the DRV vs. the traditional diaphragm valve.
Authors explain that the accumulation of flow restrictions can account for significant energy losses and that eliminating those flow barriers via full bore valves, such as the DRV, permit downsizing of process pumps and piping and increase of the processing output to a higher flow capacity.
They go on to explain that regional under pressure zones, also named cavitation, can cause significant harm to sensitive biologic drugs. In the study they observed an increased risk of cavitation for the traditional valve while there was no risk identified for the DRV.
Specific study design details and results can be found in the application note.
Summary
While improvements have been made in several areas of biomanufacturing to increase efficiency and safety, soft parts are still an area of concern. Authors present an innovative design, which incorporates the benefits of single-use, while functioning within a traditional piping construct. This permits valuable improvements without the need for full-scale retrofit of existing manufacturing. The design also provides benefits to the manufacturing process by reducing shear and pressure drop.
To see all data and learn more about the DRV, please read the full application note: