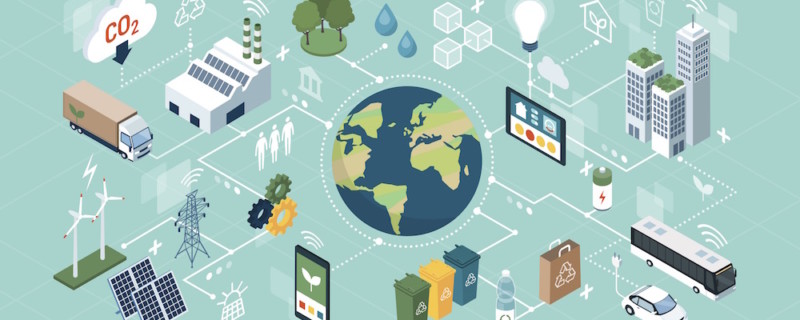
Practical sustainable processing of post-use plastics in an increasingly single-use biomanufacturing environment
The benefits of single-use technologies in biomanufacturing are undeniable. Single-use products minimize operational risk, personnel requirements and validation activities. They also reduce utilities and water cost in cleaning and sterilization, as well as batch changeover time. This last factor is particularly valuable in pilot and small-scale manufacturing where frequent changeover is often necessary. And, as more personalized products become approved, we will no doubt be seeing even smaller manufacturing lots become an increasing priority.
However, the use of single-use technologies does generate a very visible concern: plastic waste. As a result, the impact of single-use (SU) biomanufacturing has been examined extensively for its impact on the environment. In our industry we use the term “plastic” to refer to HMW organic polymers that can be molded into shape while soft and then set into a rigid or slightly elastic form. The “setting” can be accomplished by thermal, chemical or radiation action and it can be reversible or not. We use plastics in such applications as housings, tubing, and tank liners. Concern for plastic waste in general is illustrated by many recent international goals and regulations, including the May 21, 2020 directive from the Council of the EU establishing a strategy which provides for such strict restrictions as banning certain plastic convenience items entirely, and ensuring that by 2030 all plastic packaging placed on the Union market is re-usable or easily recycled [1].
On the other hand, many have observed that the issue for biomanufacturing is quite different from such simple consumer convenience items as foam food containers or shopping bags. SU biomanufacturing items provide particular and demonstrable values to society in, e.g., reducing cost and risk in the manufacturing of pharmaceuticals. None would argue about the value of disposable surgeons’ gloves or syringes, and SU biopharmaceutical manufacturing supplies can be put in the same category.
Single-use Biomanufacturing’s Environmental Impact
After much study, we now know quite a bit about the environmental stress in SU bioprocessing, as compared to conventional steel facilities. Advanced studies conclude that, for the majority of SU installations, there is actually an overall reduction in the net environmental footprint, or ecological stress, as compared to conventional glass and steel facilities. Very rigorous comparative Life-Cycle Assessments (LCA) indicate that often (rather surprisingly) SU bioprocessing technology exhibits a lower environmental impact in all impact categories examined. From terrestrial ecotoxicity, to marine eutrophication, to ozone depletion– in the long run SU-based manufacturing is equal to or even more environmentally friendly. For example, it’s been reported that operating a SU technology facility is in the order of 50% less energy intensive than one based on conventional stainless steel. This is primarily because heating highly processed water to clean and sterilize the reusable equipment consumes more energy than producing and disposing of plastic containers. Other calculations suggest that going SU results in an about 85% reduction in operational water usage and chemical waste generation.
The best analyses show that right now the majority of SU manufacturing doesn’t conflict with sustainability goals at all, but in some cases is actually superior to the conventional stainless-steel engineering it replaces. Nevertheless, there are still areas of desired improvement. Many would like to reduce the environmental stress caused by disposal of used plastic containers. The good news is that creative approaches to the problem of repurposing or recycling the plastic waste have been continually arising.
Challenges in Handling Post-use Plastic Products
Recycling plastic is not as easy as it may sound on the surface. The first challenge is the definition of terms and goals. We all want to improve our handling of used plastic material, but there aren’t even universally accepted goals to strive to. For example, much bioprocessing waste now ends up in a landfill. Would using it in a second operation (either the same activity, or a less stringent one such as in-process material storage) be an acceptable solution? What about diverting it to incineration to replace coal for power-generation? Even the generally heralded down-cycling of post-use plastic serving as a feedstock in the production of construction lumber or pallets is, by strict definitions, not truly “recycling”. And, by any definition, while very significantly reducing the environmental burden of each kilo of repurposed plastic, such downcycling doesn’t contribute to truly a “circular economy.”
Another challenge is that when it comes to recycling, not all plastics products are equal; some are more difficult to recycle than others based on their collectability as well as their chemical and physical properties. Yet, another derives from the fact that each type of plastic is normally addressed and dealt with in different ways and many bioproduction materials are integrally composed of different plastic types. In addition, the material that the plastic is contaminated by, for example pharmaceuticals or GMOs, makes shipping and handling more difficult and more regulated than other plastic waste. In spite of these challenges, we do see an increasing number of journal publications describing new, creative approaches to managing plastic waste [2, 3, 4]. These approaches include new ideas for reuse, repurposing and even true recycling plastics that are more environmentally friendly and even require less processing. And, most agree that at this stage of technology, we mustn’t let the perfect be the enemy of the good– establishing significant gains in the handing of post-use materials is a noble goal.
In general, the options available for the post-use handling of manufacturing plastics include the currently popular approaches of sending to a landfill or non-functional incineration. However, technology exists to “recycle” them by, eg:
- Using the entire object itself again in the same or less-stringent application, such as waste containment
- Recovering the object’s stored energy by direct incineration to eg, produce steam for power generation
- Recovering the stored energy using pyrolysis to produce a complex liquid mixture for such things as fuel
- Reusing the cast plastic polymer in its original state for producing such final products as lumber or roads
- Preparing and liquefying the plastic polymer (with a solvent or thermally) and employing in new product
- De-polymerizing the constituent polymer and re-polymerizing that same monomer as virgin plastic resin
- Breaking the plastic monomer down to its constituent simple chemicals for use in virgin plastic monomer
Currently, the majority of used materials from SU manufacturing are decontaminated and commercially landfilled or incinerated. Many SU suppliers are actively pursuing the development or implementation of more sustainable options for manufacturers. Here we introduce example companies commercializing new technologies as “right-now” solutions to handling post-use plastic products (“recycled”) from biomanufacturing. Each is reviewed from the perspective of how it could recycle biomanufacturing materials specifically. While none offer a perfect solution, they do represent clever, outside-the-box thinking that addresses the complex, growing problem of plastic waste as a whole. The various solutions offered conduct the waste stream in different directions and offer unique environmental burden reductions or trade-offs. Some are already providing a recycling service for biopharmaceutical manufacturers’ and SU suppliers. Whether others could provide a practical solution is a question for not only the recycler’s particular approach, but also for each manufacturer’s use of materials, used material preparation capability, and proximity to the recycling facility. The technologies are presented as examples of currently operationally possible opportunities for further exploration by individual manufacturers.
MACREBUR
MacRebur, led by its founder and CEO Toby McCartney, is working to solve two major world problems at the same time. The first is to reduce the plastic waste epidemic and second to improve poor quality roads. MacRebur does this by processing plastic waste into pellets and including them as binders, extenders or modifiers. This solution re-uses plastic waste as well as reduces the volume of bitumen required in an asphalt mix for road, parking lots and driveways. Bitumen is the fossil fuel added to the asphalt mix for pavement construction. McCartney and his team have found that by adding waste plastics to the asphalt mix they can create roads that are up to 60% stronger and up to ten times longer lasting. Finally, for every ton of bitumen that is replaced in asphalt mixes they save a ton of carbon emissions [5]
TRIUMVIRATE
Triumvirate has extensive experience in medical, hospital and pharmaceutical plastic waste recycling. They process a wide range of plastic waste types and utilize the plastic to create “lumber,” thus keeping this material out of landfills and the carbon out of the atmosphere. The plastic lumber is used in landscaping, construction, pallets, trucks and trailers. Employing a proprietary process they collect, sterilize and recycle even regulated waste. Having been in business for more than 30 years, their clientele includes pharmaceutical waste generators. They have experience assisting clients in establishing solutions that are compliant, cost-competitive, and sustainable [6].
TERRACYCLE
TerraCycle is an international leader in “recycling the unrecyclable.” Its founders have focused on using waste materials which have no value to make products that are innovative and affordable. The material they collect is turned into a raw material that is sold to manufacturers to use in new products.
One example is how TerraCycle turns plastic waste into plastic lumber. The plastic lumber components are tested for strength and structural integrity and then shipped to the manufacturer to be trimmed and finalized as needed. TerraCycle has been able to take things like flip-flops, oral care waste, and juice pouches and put them into the plastic lumber parts that are used in playgrounds and other building projects [7].
EASTMAN
Eastman provides a chemical recycling technology that converts plastic waste to usable products. They present a few distinct “now” and “near-to-launch” waste-processing technologies and platforms. Their plastic renewal technologies recycle the plastic polymer, break down some waste plastics to resin monomer or even its primary chemicals (such as H2, CO, CO2 and CH4). This latter approach allows their use as building blocks for virgin plastic resin and will provide a truly “circular economy” for plastic, with energy as the only input in the system. The company hopes to provide “an end-of-life solution” for many types of plastics, even those that can’t be processed through traditional recycling methods and are typically landfilled or incinerated. “Closing the loop of waste plastics is a complex problem that has to be solved with innovative solutions,” Eastman CEO Mark Costa said. He added that the carbon renewal technology “will revolutionize recycling at the molecular level.” This activity occurs at Eastman’s Kingsport plant, where it has modified the front of their production areas to accept waste plastic [8].
Summary
Single-use systems have been extensively studied and determined to be equal to, or in some cases, a more environmentally sustainable approach to biopharmaceutical manufacturing than more traditional stainless steel facilities. However, more can be done to ensure that the post-use plastic is handled in an environmentally friendly manner and does not end up in undesirable places.
Much is going on, and it is very encouraging to see researchers developing creative processes and chemistries and providing new options for handling plastic waste. We also applaud suppliers who are working on other sustainable biomanufacturing solutions, such as engineering more sustainable plastic resins, creating products or processes with recyclability in mind, and teaming up with biopharmaceutical manufacturers to explore options ensuring these plastics are handled well post-use.
Finally, look for future articles on The Cell Culture Dish exploring how those who are engineering biopharmaceutical facilities are improving many aspects of their design [9], including the sustainability of plant construction, operation, and decommissioning.
About the Author
William Whitford, Life Science Strategic Solutions Leader, DPS Group
Bill Whitford has recently joined DPS Group as the Life Science Strategic Solutions Leader. Here he will assist in developing creative strategies supporting the manufacturing of both classical and innovative biotherapeutics.
Bill began his carrier as an R&D Leader, commercializing over 40 distinct products supporting biomedicine and biomanufacturing. Applications ranged from assisted reproduction to the culture of animal cells in protein biological and vaccine production.
Most recently Bill has been a thought leader identifying burgeoning biomedical products and processes. An invited lecturer at international conferences, he has published over 300 articles, book chapters, and patents in bioproduction; is a regular presenter at international conventions; and is an instructor in biomanufacturing.
Footnotes
-
1. www.consilium.europa.eu/en/press/press-releases/2019/05/21/council-adopts-ban-on-single-use-plastics/#:~:text=The%20EU%20is%20fighting%20marine%20plastic%20pollution.&text=One%20of%20the%20main%20purposes,will%20be%20banned%20by%202021
-
2. www.thebalancesmb.com/top-recycling-industry-publications-2878014
-
3. phys.org/news/2020-06-method-recycling-plastics.html
-
4. phys.org/news/2020-05-circular-economy-plastics-plastic-pollution.html
-
5. www.macrebur.com/
-
6. www.triumvirate.com/services/waste-disposal-management/industrial-waste-recycling-solutions
-
7. www.terracycle.com/en-US/pages/playground
-
8. www.eastman.com/Pages/Home.aspx
-
9. www.dpsgroupglobal.com/news/2020/7/construction-management-considerations-post-covid-19-for-life-sciences-and-semiconductor-manufacturing-facilities-/