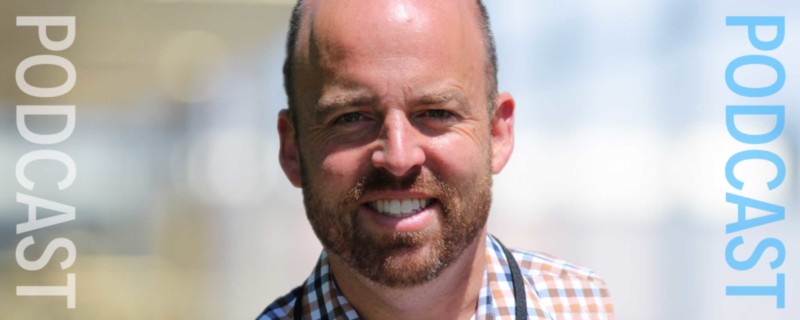
Raw Material Quality – Identifying and Mitigating Variation
Podcast: Download (Duration: 17:29 — 24.0MB)
Subscribe Here: Apple Podcasts | Spotify | RSS | More
Subscribe to the Cell Culture Dish Podcast on: iTunes | Google Play
Show Notes
I began the interview with Cory by asking about how we have seen raw material quality evolve, where we are at now and where we are heading. He explained that over the past decade we have developed a greater understanding about how raw materials impact final product quality and that this has been possible due to new analytical technologies. These new technologies have enabled higher resolution and better detection of both purity levels and which impurities are present. He went on to say that better tools for collecting, analyzing and reporting on large data sets have been critical in developing a better understanding of raw materials and permitting characterization. This has in turn led to a better understanding of the manufacturing process and has led to a more defined and optimized process.
Next I asked how we can further utilize technology across the supply chain to identify possible sources of variation in raw materials and also how to increase process and raw material control. Cory stressed the importance of partnership between stakeholders. There must be good communication between the end users, suppliers and the raw material suppliers so that when there is an issue, the cause can be determined and companies can work together to make necessary changes. One thing that can help with this is electronic or digital data exchange. There are new standards that have come out the last couple of years and we need to implement these as an industry, for example, the ASTM standard. By exchanging data via electronic or digital means, we can achieve better raw material control. Cory went on to say that first it is important to identify when variation is present, then through characterization, we can determine what levers are available to influence change. Lastly by applying analytics, we can measure the effects of the changes that we have made.
We then discussed the biggest problems that raw material variation can cause in biomanufacturing, with the primary issue being a failed product. Cory explained that the loss of a batch is extremely costly in terms of money, time and resources.
Then I asked Cory what he saw as the most effective methods for mitigating raw material variation. He said that using an approach that combines all the measures he had mentioned previously is best. He stressed again that partnership is important. Letting raw material suppliers know in advance about any special issues related to using the raw material in biomanufacturing can help these suppliers understand any potential pitfalls. Then data that has been collected around specific raw materials’ quality profiles can be used when working with the raw material supplier to solve an issue. For example if the raw material supplier is sourcing a raw material from multiple locations and one location provides higher quality material, then this information can be used to only use material sourced from certain locations. This can only be discovered through understanding the raw material source and the amount of variation present in each sample. Physical and chemical testing can be used to characterize purity and impurity profiles of raw materials from different sources and functional testing can tell us what the impact is on the culture. Furthermore by using a database, we can understand variability of available material and can use that toward smart manufacturing and selecting the raw materials that work best in our process.
We moved on to discuss the use of data collection and real time, in-process analytics to impact raw material quality. Cory said that data collection helps to identify the most immediate need and to further understand what issue the raw material quality is causing. Increased analytical capability means decreased variability and and overall increase in quality and consistency of raw materials.
Last, I asked him about the best way for suppliers and end users to work together to ensure raw material quality. He said that in the past it has taken multiple end users working together with suppliers to effect change. Raw material suppliers often see the biopharamceutical industry’s share of wallet as very small and in turn this hinders the ability to make changes. In some instances, the food industry or others provide a much bigger demand, thus companies in the biopharmaceutical space must join their voices together to be significant enough to push for necessary changes.
I closed by asking if he had anything else to add for listeners. Cory said that another area that is important to consider is material specifications. Sometimes material specifications just exist because that is how it has always been done. We need to ensure that the specifications are meaningful and relate to quality attributes. For instance, an appearance specification may not be very important, as what it looks like doesn’t matter to the cells and also it is very subjective. In contrast, specifications around particle size and solubility, while they might impact appearance, are much more objective and measurable.
For more information on raw material quality, please see the eBook – Raw Materials Management