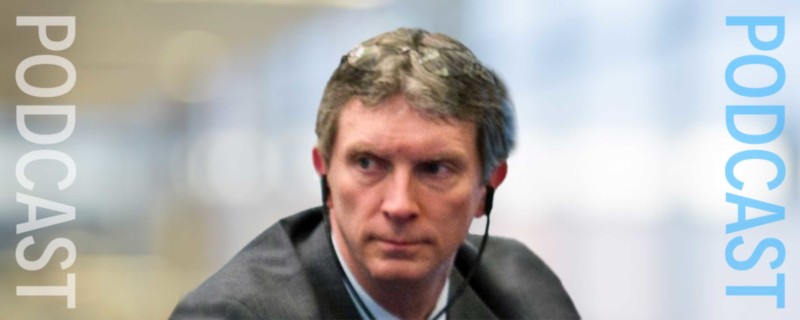
Single-use Bioreactors for Fermentation – It’s now a reality that deserves consideration
Podcast: Download (Duration: 12:31 — 17.2MB)
Subscribe Here: Apple Podcasts | Spotify | RSS | More
Subscribe to the Cell Culture Dish Podcast on: iTunes | Google Play
Show Notes:
I began the interview by asking Mr. Clapp about why we have seen such an increase in adoption of single-use technologies in cell culture biomanufacturing, but not in microbial fermentation. He explained that microbial fermentation is more demanding on equipment. As single-use technologies matured and successful implementation was demonstrated in cell culture applications it opened the door for wider adoption including more challenging cell culture applications. The business benefits also became apparent, in particular the way single-use could better adapt to changing market conditions. Once wider adoption and business benefits were proven in cell culture applications, interest increased in using it for microbial fermentation.
Next, I asked Ken to summarize some of the key benefits for using single-use technologies in fermentation. He said that the benefits are largely analogous to the benefits found in cell culture applications. Primarily, reduced cost for capital equipment and the supporting utilities and piping, and reduced footprint. Another big benefit is better equipment utilization due to reduced batch turnaround time, with no issues around product cross contamination, no CIP or validation. Lastly, it supports a scale up or scale out model, which gives manufacturers a great deal of flexibility in their business model.
I was curious, if I was using stainless steel tanks now, what factors would I have to consider in deciding on a move to single-use. Ken explained that single-use fermentors may not be appropriate for all fermentation processes, just like single-use isn’t a good fit for all cell culture processes. He explained how to screen process requirements against the capabilities of the equipment and to look at the biomanufacturing strategy with the therapeutic product being produced.
Then we talked about implementation of single-use fermentation. Ken said that from a high level, implementation looks similar to stainless steel minus some of the space requirements. Fluid management, tubing sets, tubing welders for single-use may be foreign to stainless steel users. This means training, particularly in bag handling and other topics unique to single-use is needed. The amount of training depends on the familiarity of the operators and the companies with single-use technologies.
I then asked about how fermentation could leverage the experiences in cell culture to speed adoption. Ken said that there is a vast body of knowledge from cell culture that can now be applied to fermentation. He discussed how concepts like process screening, technology transfer, equipment design and supply chain maturity can be leveraged.
Lastly, I asked Ken if he had anything he’d like to share with listeners in closing. He said that he started his career in conventional systems ranging from 500 mL to 40,000 L and 15 years ago he wouldn’t have believed that single-use bags could provide the same level of performance as stainless steel, especially in fermentation. Then seven years ago he saw his first single-use fermentor that had already been in use for three years doing contract process development and manufacturing work. It was able to handle the three biggest challenges that Ken saw for single-use fermentation: oxygen transfer, power input, and metabolic heat removal. This system convinced him that single-use fermentation was possible. Since then the market has seen the benefits of single-use and the growing need for this technology.
For more information on microbial fermentation, please see part 2 of this podcast:
Implementation of single-use bioreactors for microbial fermentation is easier than you think