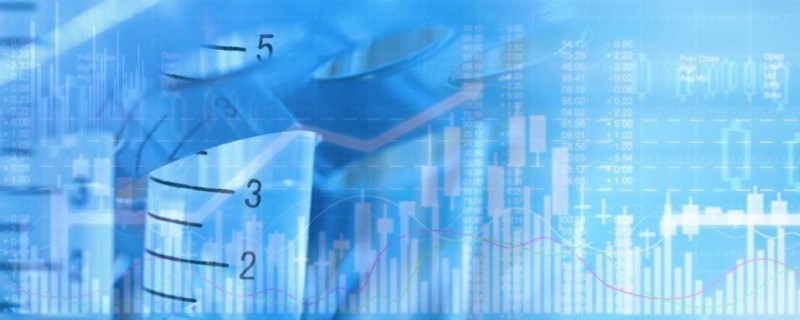
Single-Use in Biotech – Addressing Opportunities and Challenges
Contributors:
Over the past decade, the growth and adoption of single-use technologies in biomanufacturing has been steep and sustained. What began primarily with single use bioreactors has expanded to include single-use components from early upstream processes through downstream and into commercial manufacturing. As of 2018, single-use systems were being used for about 85% of preclinical and clinical biomanufacturing and are increasingly being incorporated into commercial manufacturing1. The benefits of single-use technologies have been well documented and include risk mitigation, increased efficiency, reduced personnel requirements, less validation time, and customizable solutions. The technology has also been found to reduce utility and water costs for cleaning and sterilization, as well as lower batch changeover time. This is particularly important for facilities that run smaller manufacturing lots, with several different products or are looking to maximize facility flexibility.
Single-use Bioprocessing Market
As the benefits of single-use have become clear and adoption has increased, the market has seen significant growth. The global single-use market was valued at USD 15.8 billion in 2020 and is expected to expand at a compound annual growth rate (CAGR) of 16.0% from 2021 to 20282.
Growth of new therapeutic modalities, such as cell and gene therapy and antibody drug conjugates are increasing demand for single-use solutions. This has also led suppliers to launch new single-use products to meet the specific needs of these modalities. Thereby driving the expansion of single-use products and growth of the market.
There has also been a desire by end users to achieve end-to-end single-use solutions, thus driving suppliers to create both upstream and downstream single-use products to address each step of the biomanufacturing process. Single-use simple and peripheral products, including filters, tubing, transfer systems and connectors accounted for the largest revenue share, 49.0%, in 20202.
While single-use products for the upstream workflow segment represented 57.0% of the revenue share in 2020, suppliers are advancing implementation in downstream with more recent introductions of pre-packed chromatography columns, filtration devices, pumps, heat exchangers, etc.2.
Overall end users have been moving toward manufacturing solutions that are adaptable to demand fluctuations, have lower capital cost investment, are at smaller scale and can be duplicated for localized manufacturing.
Effect of Covid-19 Pandemic on Single-use Technologies
Like most industries, the Covid-19 pandemic impacted biomanufacturing with both positive and negative effects. While some industries struggled with lower demand for products, during the pandemic, biopharma had the opposite experience with demand for new therapeutics for Covid-19 vaccines and treatments surging. Positive outcomes were that the biopharmaceutical industry delivered highly effective Covid-19 vaccines in record time and mRNA technology was proven successful and safe, thereby opening the door for its use against other viruses and in other applications, including oncology and gene therapy. Treatments for Covid-19 infection were also approved with several others in the pipeline. All this was achieved while still maintaining production of approved medicines for patients.
There have been negative impacts as well, including in the near term, the prioritization of pandemic related therapeutics over non-pandemic related. The impact of pandemic prioritization of resources including supplies, manufacturing capacity and staff is not yet fully understood, but may delay therapeutics for other non-covid illnesses. Another near-term impact has been supply chain shortages with a sharp increase in demand for bioprocessing supplies related to Covid-related therapeutics in addition to existing resources being prioritized for pandemic related projects. In the long-term investment by both nonprofit organizations and governments as well as investors has led to an influx in funding that will support investment in increased manufacturing capacity, R&D pipelines, supplier product innovation, etc.
Specifically related to single-use technologies, demand for single-use process solutions and facilities increased significantly during the pandemic, due to the speed, flexibility, and lower capital investment that single-use provides. Due to the increase in single-use product demand, end users and suppliers are concerned about ongoing and future shortages, in addition there is already a worldwide shortage of some of the key high-purity polymers causing increased lead times3. In a recent survey conducted by BioPlan Associates, shortage of single-use systems and other supply issues were a top concern in bioprocessing post Covid-19, with 75% of biopharma respondents and 70% of supplier respondents listing it3. It has been reported that end users are currently facing long delivery times for both single-use equipment and consumables. Often vendors can deliver single-use equipment within a couple of months, but consumables can take up to fourteen months due to required supplier support for Covid-19 vaccine and therapeutic production4. Furthermore, many equipment suppliers have single source supply chains because of their proprietary solutions, which also impacts the ability to increase supply quickly, as does facility and workforce constraints4.
Single-use Systems – Opportunities for Improvement
While the pandemic has created some challenges for single-use products with respect to supply, some supply issues as well as other challenges existed prior to the pandemic. Looking forward there are several areas where the use and implementation of single-use systems could be improved.
STRENGTHENING THE SUPPLY CHAIN
Some materials used in the manufacture of single-use technologies are prone to shortage and were difficult to source even before the pandemic. The pandemic prioritization of single-use products exacerbated these shortages and created lengthy product wait times. Thus, the supply chain needs to be strengthened with a focus on secure, readily available supplies and increased supply redundancy. Coordination between supplier and customer will be essential to ensure continuous supply of critical products. Relatively speaking there are not that many suppliers of much needed single-use products, thus it may become important to move toward less proprietary and more open or agnostic processes so that multiple vendors can be leveraged to provide a solution, thus permitting quicker deliveries4. Customers may seek to avoid a proprietary solution that creates a single source of supply, especially for consumables.
Liquidyne circumvents supply chain issues by utilizing blanket orders, which allows the supplier and end-user to understand product needs for a set period of time, thus permitting procurement of the appropriate supplies upfront.
CUSTOM FIT FOR PURPOSE SOLUTIONS
Along the same line, collaboration between suppliers and end users for single-use processes will become increasingly important as suppliers will need to work with customers upfront to understand issues and concerns as well as their short-term and long-term vision. This will include ensuring that the process and required single-use components and consumables will be available to meet product demand and account for increases to scale.
One of the major challenges to custom fit for purpose solutions is technological incompatibility. While all single-use consumable products serve a similar purpose, design differences and differences in material components can complicate product selection and validation particularly if components from multiple suppliers are used in the same single-use system or if different single-use systems are used at different manufacturing sites in the same organization. Liquidyne has partnered with Agilitech, a leading single-use solutions provider to aid customers in designing and implementing state-of-the-art equipment and bioprocessing systems for biotech research labs through to full-scale production, along with game-changing bioprocess engineering and automation services. Through this partnership, Liquidyne and Agilitech can provide clients with customized solutions that meet their specific process requirements and deliver a fit-for-purpose solution.
Market-leading suppliers offer a range of competitive single-use systems with some flexibility within their platform of products. However, full flexibility of these products is often limited: they are flexible in that they are single-use, facilitating quick and sterile batch changes between production runs, but the instruments themselves are not always adaptive to unique process needs and typically do not integrate products and/or components outside of brand5. There is a need in the industry for more flexible solutions where products can be interchanged to some degree as this permits more customized solutions as well as provides alternatives when supply shortages of one product occurs. Liquidyne works with a host of suppliers, to ensure their clients have access to selection of products that fit best their process.
CUSTOM SOLUTIONS AND COLLABORATION IN PRACTICE
Liquidyne takes a unique approach to creating a customized process for end users. They leverage expertise in unit operations and quality management to ensure each single-use process is simplified and meets customers’ exact process needs now and for the future. They achieve this by beginning with a clear understanding of the customers’ process and project prior to creating the assembly. Their team of process experts work to decipher and optimize all requirements including timeline and budget. Then the design team takes this information and produces 2D CAD drawings for collaboration and review. Lastly, single-use technology parts are acquired for assembly and development of a prototype, small batch, or production. By having access to a wide range of supplier options, they can source parts from over 20 different vendors. This helps to alleviate any supply chain challenges and permits dual vendor qualification, and they are not limited to the same supply chain constraints that single vendors are.
STANDARDIZATION OF SINGLE-USE SYSTEMS
There are a large variety of single-use products and suppliers. As a result, suppliers have used different materials and components in manufacturing. These differences have created a lack of standardization which requires that end users that opt for a combination of products from different suppliers will have a more challenging and lengthy validation process. In particular, it makes extractable and leachable studies complex.
Thus, organizations including the Bio-Process Systems Alliance (BPSA) and the BioPhorum Operations Group (BPOG) are looking at how the industry could introduce a level of standardization across single-use systems that would ultimately streamline the supply chain and reduce development times for end users. This in turn would lower cost and improve product quality. Standardization would not mean that everyone would use the same exact equipment with the same design, as flexibility to ensure the correct process is important. Instead, it is about adopting common business and technology practices that would streamline work for the end user6. Aligning and standardizing means simplified process validation, reduced inventory requirements, straightforward training programs, less operator errors and increased automation options. Supplier and end user collaboration found in BPSA and BPOG, have enabled the development of important best practice guidelines such as the single-use user requirement (SUUR) template and the technical diligence template and the supply chain template, all designed to ease the burden on end users and align end users and suppliers and create frameworks from which both can work from7.
INCREASED AUTOMATION
To increase efficiency, reduce error and reduce manual tasks, automation will need to be incorporated into single-use systems. Creating solutions based on open architecture control systems means the systems are not proprietary and can be supported by the customer’s in-house automation team, which provides customers the flexibility to go from a standalone control capability to a distributed control architecture in the future4. In addition, biomanufacturing staffing has been stretched very thin, an issue that could be improved with more automation of routine operations.
SUSTAINABILITY – ADDRESSING ENVIRONMENTAL IMPACT
The use of single-use technologies does generate plastic waste. As a result, the impact of single-use (SU) biomanufacturing has been examined extensively for its impact on the environment. In the industry the term “plastic” refers to HMW organic polymers that can be molded into shape while soft and then set into a rigid or slightly elastic form8. Currently, most used materials from SU manufacturing are decontaminated and commercially landfilled or incinerated8. Many SU suppliers are actively pursuing the development or implementation of more sustainable options for manufacturers.
A recent study, “Streamlined life cycle assessment of single use technologies in biopharmaceutical manufacture,” looked at the environmental impact of a single use 2000L scale biological bulk drug substance manufacturing process9. Notably, the results showed that the largest contributor to environmental impact on single use technologies was the electricity required for plant operation and environmental footprint with respect to plastic waste was found to be extremely small. Authors suggest that methods to increase process efficiency, like process intensification, could reduce plant operation time may be one of the best strategies for reducing the environmental impact of biologics manufacturing.
CONTINUED SPECIALIZATION OF PRODUCTS FOR CELL AND GENE THERAPY APPLICATIONS
Cell and gene therapy manufacture has been identified as an area of growth for single-use systems. However, several of these cell and gene therapy processes still use products that were created for antibody production or the medical device field. While new products have been introduced that are fit for purpose, there is still a shortage of end to end single-use process solutions particularly ones designed for the appropriate scale. In response, developers have had to patch together technologies designed for traditional protein biologics or borrow from the medical device field to create solutions. Since these technologies were originally designed for a very different type of workflow, they may not fit the needs of cell and gene therapy well and this can lead to an inefficient and costly workflow5.
Conclusion
In summary, single-use systems offer many benefits for biomanufacturing over more traditional stainless-steel facilities. These benefits have increased in demand and as a result supply has been strained and custom solutions are required to meet customer needs now. Companies that offer end users custom solutions provide valuable insight in creating systems that address component incompatibility, supply chain constraints, and fit for purpose requirements while at the same time help their customers ensure that the system can evolve to meet future needs.
Looking forward there are areas of improvement to be addressed so that single-use systems can continue to deliver the tremendous benefits they offer and can move the industry forward with highly flexible, efficient, and productive manufacturing systems.
About Liquidyne
Liquidyne Process Technologies, Inc. is a leader in single-use and sanitary process equipment & components for fluid transfer, measurement, and control. We are dedicated to helping growing companies keep their fluid transfer process clean, modern, efficient, and running smoothly. We design, develop, and deliver custom fabricated assemblies and distributed products including custom single-use assemblies, tubing, hoses, stainless, mixers, valves, pumps, and more. Our reputation for quick, responsive, and knowledgeable service means you can count on us to provide intelligently engineered solutions for all your sanitary process equipment and fluid handling needs. Visit liquidynusa.com for more information.
Liquidyne Process Technologies, Inc
11925 W Interstate 70 Frontage Rd N
STE 700
Wheat Ridge, CO 80033
Footnotes
-
1. Langer, E.S., et al, 15th Annual Report and Survey of Biopharmaceutical Manufacturing Capacity and Production, BioPlan Associates, 511 pages, April 2018.
-
2. Single-use Bioprocessing Market Size, Share & Trends Analysis Report By Product (Probes & Sensors, Simple & Peripheral Elements), By Workflow (Downstream, Upstream), By End-use, By Region, And Segment Forecasts, 2021 – 2028. Grandview Research: San Francisco, CA, May 2021;
-
3. Rader RA, Langer ES, Jhamb K. COVID-19 Impact on Bioprocessing: Accelerating Trends and Long-Term Impact of Novel Coronavirus-19 on Biomanufacturing and Bioprocess Supply Chain. BioPlan Associates: Rockville, MD, June 2020; https://bioplanassociates.com/wp-content/uploads/2020/07/Covid-19-Impact-on-Bioprocessing-White-Paper-BioPlan-20200605.pdf.
-
4. Downstreamcolumn.com/addressing-increasing-demand-single-use-technologies-supply-chain-shortages-future-proof-systems/
-
5. downstreamcolumn.com/future-proof-bioprocesses-flexible-single-use-technology-adapts-evolving-industry/
-
6. themedicinemaker.com/manufacture/standardizing-single-use
-
7. www.biophorum.com/resource/single-use-systems/
-
8. cellculturedish.com/practical-sustainable-processing-of-post-use-plastics-in-an-increasingly-single-use-biomanufacturing-environment/
-
9. Kristi Budzinski, David Constable, Daniel D’Aquila, Phillip Smith, Sri R. Madabhushi, Andy Whiting, Tom Costelloe, Michael Collins, Streamlined life cycle assessment of single use technologies in biopharmaceutical manufacture, New Biotechnology Volume 68, 2022, Pages 28-36, ISSN 1871-6784, https://doi.org/10.1016/j.nbt.2022.01.002.