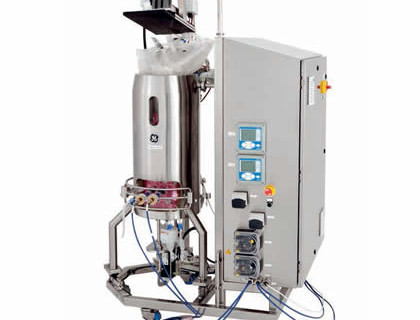
Single-use Technology for Microbial Fermentation
Microbial fermentation processes are used for biomanufacturing of various drugs and vaccines, such as hormones, antibody fragments, and pneumococcal vaccine. Stirred-tank fermentors up to 100,000 L scale have traditionally been used in such microbial processes and their success has formed the general engineering foundation and principles of the design of bioreactors. The majority of today’s fermentation processes are performed in bioreactors constructed of traditional materials such as stainless steel. However, there is an increased interest in disposable technology to gain flexibility, save batch change-over time, and minimize cleaning and cleaning validation efforts.
To date, single-use stirred-tank bioreactors for mammalian and insect cell cultures have been successfully used in scales up to 2,000 L working volume and are installed in both clinical and commercial drug manufacturing facilities. In mammalian and insect cell applications, relatively few engineering challenges for heat removal, O2 mass transfer, and process control have been detected. For fast-dividing bacteria, fungi, or yeast, however, fermentors need to be designed for very high metabolic rates. Aerobic microbial cultures typically grow 20 to 75 times faster than mammalian cells, with a doubling time of 20 to 30 minutes for some species. Such growth rates equal 20 to 75 times the heat evolution and oxygen demand of mammalian cells. To withstand the tough conditions that come with the requirements of microbial cultures, conventional bench-top fermentor systems are constructed of jacketed glass or stainless steel. For larger volumes, the primary construction material is stainless steel. Stainless steel fermentors, for example, can handle overpressures of 1 to 5 bar, which can be necessary to meet the oxygen demand of some microbial cultures.
Design challenges for single-use fermentors
The construction of single-use bioreactors suitable for fermentation processes poses significant engineering challenges. One such challenge is reduction in culture heat load caused by the insulating properties of the single-use film.
The net heat load in a fermentor is the sum of the agitation power, metabolic heat from the culture, evaporative cooling at liquid surface, sensible heat in the gas stream, and heat loss to the environment [1]. For microbial systems, however, sensible heat and evaporative cooling can be neglected as they are relatively low. Heat loss to the environment is also low because of the outer vessel wall insulation. Consequently, heat from agitation and culture metabolism contribute the most to the culture heat load.
As a single-use polymeric liner has a lower heat transfer coefficient compared with stainless steel, the heat transfer rate of single-use fermentors is significantly lower compared with conventional stainless steel fermentors. Depending on the liner thickness and formulation, the heat transfer coefficients of single-use fermentors are approximately half the ones of traditional stainless steel bioreactors. The reduced heat transfer rates pose an increased challenge to maintain a suitable temperature for fast growing microbial cultures in single-use fermentor systems. Lower surface area-to-volume ratios at larger scales further aggravate the heat removal challenge. To compensate, the following points can be considered:
- Adequate agitation to provide convective turbulent flow to all heat transfer surfaces.
- Include additional design solutions for cooling, such as spiral-baffled or segmented tank jackets, jacketed bottom and top dishes, and auxiliary heat-removal surfaces.
- Increase vessel height-to-diameter ratio to concomitantly increase the surface-to-volume ratio.
- Use of low-temperature coolants such as ethylene glycol.
- Pre-cooling of the sparge gases (not very effective, though, as gases have a relatively low thermal heat capacity compared with liquid coolants).
- Decrease growth rate to reduce metabolic heat generation by limiting carbon source feed rate. This solution has a dual effect. As the oxygen demand will be lower, the agitation needed (and heat generated) to maintain a sufficient level of dissolved oxygen will be decreased.
- Apply continuous culture. This solution reduces the fermentor size and consequently maximizes the heat transfer surface-to-fermentor volume ratio.
Another challenge when designing single-use fermentor systems is obtaining adequate oxygen mass transfer to support high-density cultures. Single-use fermentors do not suffer from any inherent design or material limitations for oxygen transfer from the gas to the culture liquid. To date, most features available for glass and larger-scale stainless steel systems are also available for 50 L single-use fermentors, with exception of high head space overpressure. Single-use fermentors larger than 50 L, however, will require power/unit volume agitators of sufficient size to maintain the oxygen transfer rates necessary to meet the oxygen demands of high-density microbial cultures.
Aspects to consider for increasing the oxygen mass transfer include:
- Increasing power of the agitation system [2]
- Oxygen enrichment of sparger gas
- Use of microporous spargers (addition of antifoam agent might be necessary)
- Increasing head pressure (will require a hardware support structure to hold the single-use bag, but might be redundant with today’s design solutions)
Conclusion
The engineering challenges in terms of heat removal and oxygen transfer delayed the entry of disposable stirred-tank fermentors. Since 2007, however, when the first single-use microbial systems were introduced, successful high-cell density cultivations of both E.coli and Pseudomonas have been reported [3]. By applying general bioengineering principles and designs, high oxygen transfer rates can be achieved also in disposable fermentors. Augmented designs and operational methods compensate for the low heat transfer rates in these systems. Although pressurizable single-use stirred-tank fermentors are within the realm of technical feasibility, this feature might not be necessary as sufficient oxygen transfer can be achieved through a variety of mechanical and process control designs and techniques.
Footnotes
-
1. Wang DIC, Cooney CL, Demain AL, Dunnill P, Humphrey AE, Lilly MD, Fermentation and Enzyme Technology: John Wiley and Sons, New York, pp. 69-70(1979).
-
2. single-use-bioreactor-mixing-how-to-meet-familiar-requirements-with-novel-technologies/
-
3. Application note: Microbial fermentation in single-use Xcellerex fermentor system. GE Healthcare, 29-0564-39, Edition AB (2014)