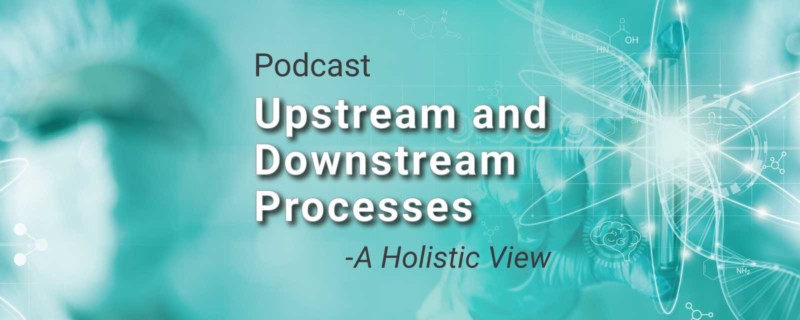
Upstream and Downstream Processes – A Holistic View
Podcast: Download (Duration: 14:15 — 11.4MB)
Subscribe Here: Apple Podcasts | Spotify | RSS | More
Subscribe to the Cell Culture Dish Podcast on: iTunes | Google Play
Hosted by: Brandy Sargent
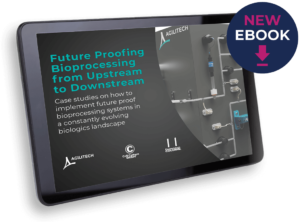
“ Future proofing Bioprocessing from Upstream to Downstream”.
You can download all the articles in the series, by downloading the eBook.
Not everyone has the luxury of building from the ground up. How do you create a unified system between upstream and downstream with existing equipment and processes? And if you have the ability to build from the ground up, how can you ensure that your design is future proof? We spoke with Phil Sanders, Biotech Chief Innovation Officer from Agilitech, to develop a set of best practices for creating a holistic process from upstream to downstream.
Create a Growth Plan with Scalability Built in
When companies are developing their process, it is easy to have a more myopic view of focusing on what is needed right now. Unfortunately, from a planning perspective this is very difficult because what is needed now often doesn’t work as companies need to scale up. When Agilitech works with customers, they ask customers to help them envision what their needs will be 3 years from now, 5 years from now, and at full commercialization. These answers are critical for decisions that companies will make right now. Because speed and cost are two driving factors, especially at the beginning of operation, companies often look for what is available now and what is the most cost-effective option. However, later they may learn that the process that they have created can’t scale up or can’t meet other process or quality related requirements. At that point, companies frequently wish they would have made different decisions earlier that took future needs into consideration.
One thing that Agilitech is helping customers with is bringing a holistic view. For instance, even if the project is related to upstream, it is important to think about what is the downstream going to look like. What will it look like in a process development environment, how about a manufacturing environment? Thinking about the scalability earlier in the process allows room to build scalability into the design for the future.
It is common in an industry that is always pushing for speed and efficiency to think about what must be produced now, but later customers often realize that they have wasted a tremendous amount of time creating a process and buying equipment that will ultimately need to be replaced for something that is more scalable or flexible; therefore, off-the-shelf is not always the best solution, even if it serves the purpose in the moment.
Don’t Get Locked into a Proprietary Solution – Remain Brand Agnostic
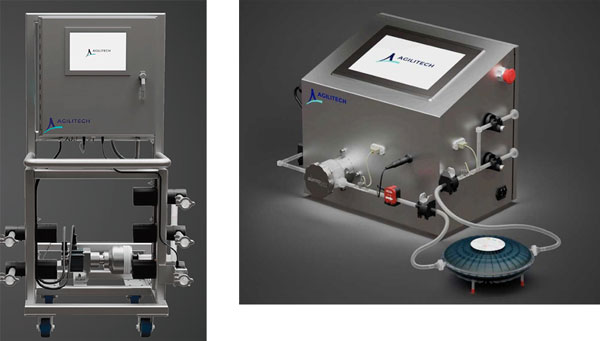
The benchtop option (up to 3 LPM) and larger system (up to 90 LPM) both adapt to virtually any external filtration system They can be used for multiple applications including sterile filtration, depth filtration, or virus filtration. Fit-forpurpose options permit reconfiguring the flow path to add more inlets, outlets, and more.
It can be tempting to lock into a single brand or a proprietary solution for your process needs from a convenience or discount standpoint. However, there are several reasons why you may want to remain brand agnostic.
Locking into a single solution may limit the process in the future. Often locking into a platform that works now results in limits on equipment size and volume that require redesigns that are costly and time consuming. A brand-agnostic approach allows companies to create a process that is flexible where all equipment works well together and communicates well across the entire process.
Proprietary software can be extremely limiting in scalability and working with other systems, particularly between upstream and downstream. Companies can find themselves in a situation where they must add another control system to expand their process for a more scalable solution.
Proprietary solutions can also impact support and whether updates and changes can be done in house or if outside help assistance is required. For instance, when using proprietary solutions, customers often find themselves relying on a specific company to provide product assistance and repairs; if customers remain more agnostic, it allows for much of this work to be done in house.
Early investment in a proprietary system often ends up being wasted because the right platform is not chosen for the long term and a proprietary solution may not permit easy substitution of another brand equipment.
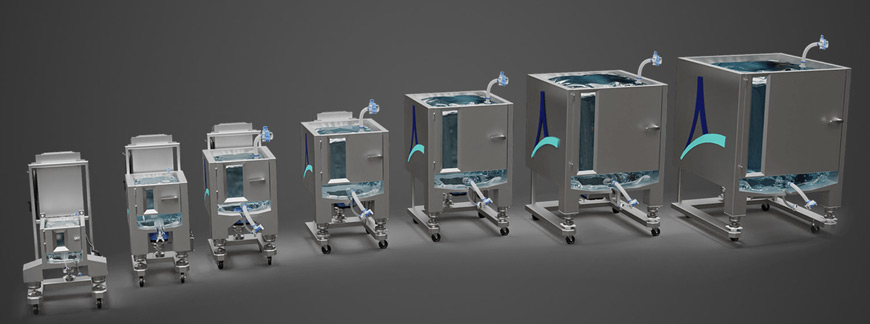
Agilitech single-use mixers provide flexibility in scale with 7 models from 10 L to 650 L. There is even a mixer available to support small-volume to full-scale production applications. The brand-agnostic design permit single-use bags to be customized to meet specific application requirements, including inlets, outlets, and sample ports. Analytical measurements such as pH, conductivity, and dissolved oxygen can also be added.
Plan for the Automation Environment
Increased automation continues to be an important trend in biologics as it enables increased process optimization, implementation of Process Analytics Technology (PAT) approaches and Quality by Design (QbD) initiatives, and helps to maintain aseptic, closed manufacturing by automating sampling procedures. When companies are starting out, they are working at a smaller scale then they will be at clinical or commercial manufacturing and many times they are still figuring out their process. This can lead to equipment purchases that save time or money. The problem with this approach is that it does not consider future integration needs or the kind of capability that they will eventually need. If the product is successful and increases in manufacturing need to occur, it will be much more costly and time consuming to make the changes later in the process. For instance, it may cost an extra $5,000-$10,000 to set up the SCADA system infrastructure up front, but once in place, companies can add to it as needed and there is an existing framework. Waiting to do this in the clinical or commercial phase will cost significantly more and will likely result in some level of process redesign. This is also an important part of how upstream and downstream process groups will communicate, so building this framework up front will facilitate communications both in process development and eventually manufacturing.
In addition, while using an industrialized platform like DeltaV™ or Rockwell Automation® will cost more up front in comparison with a proprietary automation platform, in the end scaling up on something standardized will be much simpler than using something proprietary. For example, a recent customer in the cell based protein market decided to employ an industrialized platform for just two small bioreactors, knowing that in the future they can easily scale this system up to meet their needs. They can also replicate this system as many times as needed for manufacturing. Ultimately if a company is looking to manufacture a product at market scale, they will eventually need to automate that platform and will likely use an industrialized platform. Best to start with the industrialized platform and grow from there.
Balance Speed with Designing for the Future
There is an understandable drive to speed the process, especially speed to clinic. Often companies look to how they can get up and operational as soon as possible. However, it is important to balance this desire for speed with the need to plan for the future. It is important to look at the big picture and plan a process that works today and in the future. Saving time now could end up costing time and money later. It is important for companies to work with suppliers who will create a proposal that takes future scale into consideration and will suggest processes that can grow each step toward commercialization. At Agilitech, a proposal is created that shows companies how to build a process that will grow with them, including cost considerations and a scaling plan that lets customers know what their upfront investment is along with estimates for future expansion.
Agilitech sees this issue frequently with tangential flow filtration (TFF) skids — and creates flexibility that enables customers to use different size tubing that meets their needs now and allows for future expansion. Instead of having to purchase a new skid later, it is posible to design one that will be flexible and future proof. It is important to note that companies do not have to sacrifice timelines for these solutions. Agilitech can turnaround a tailored solution like that in six to seven months, which is a typical lead time in the market today. Thus, enabling design for the future while still maintaining very fast timelines.
Leveraging Industry Standards
Another aspect of designing for the future is leveraging all the industry standards that are available. Everything Agilitech builds is to ISA 88 batch standards, which means that different levels of automation can be employed. If a customer wants something that is very manual, there are control modules for valves, pumps, and transmitters that can be built in so that everything becomes a manual operation. However, this also provides the ability to use that platform as the foundation for future growth. Equipment modules or operations can be put on top of that platform to the point where recipes or batch can be used to control the process. Following good manufacturing processes such as GAMP forces you to examine the process and ensures the development of a functional specification that defines how the unit or process will operate. Using these standards, all specifications are driven to completion before the implementation starts so that everyone is on the same page.
Future Proofing for Emerging Technologies
It is important for cell and gene therapy companies to have solutions that really fit their needs now and in the future. Many solutions are designed for much larger scale operations. Agilitech is working to provide these companies with smaller scale solutions. For example, having a single-use 10 L or 25 L mixer is really important for these companies, they can’t utilize a 650 L or 1,000 L mixer. Agilitech offers chromatography skids that are among the smallest units on the market to support these emerging technologies at the scale that they need. At the same time, Agilitech is gaining insight into these processes and thinking about how solutions can be created to resolve other issues that these companies are having, including other products that need to be scaled down to meet their needs.