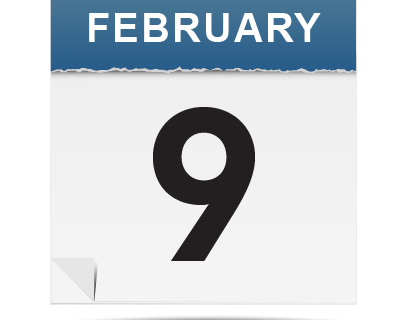
The Dish’s Weekly Biotechnology News Wrap Up – February 9, 2018
This week’s headlines include: Cancer Immunotherapy is getting even better, Sunovion Parkinson’s Drug Heads to FDA, Setting Up Battle With Acorda, FDA agrees to quick review of smallpox drug, Abcam, Molecular Devices join forces to develop immunoassays for researchers, Cobra Biologics and Symbiosis granted £1.9 million from Innovate UK, Corning and CytoSMART collaborate to simplify cell counting in laboratories, and Bristol-Myers’ positive cancer data still lags Merck.
In Case You Missed It, Recent Articles on Cell Culture Dish and Downstream Column:
Is Continuous Biomanufacturing a Good Fit for Your Process? – Continuous Biomanufacturing Implementation – Frequently Asked Questions
We recently finished our Ask the Expert discussion, “Ask the Expert – Implementation of Continuous Manufacturing Strategies for Protein Therapeutics.” During this Ask the Expert session, we covered several common questions related to continuous biomanufacturing, including PAT initiatives, expected timelines, potential cost savings, optimization, process parameters, and lot release and how it compares with traditional fed-batch processes….
A High Throughput System for CAR-T Cell Screening in Tumor Spheroids
Chimeric antigen receptor (CAR)-T cells which are engineered to recognize tumor cell-specific surface antigens, have shown promise to affect complete remission in patients with B-cell malignancies. With the recent FDA approval of Novartis’ Kyrmriah™ and Gilead Science’s Yescarta™, CAR-T Cell Therapy could be on target to become the standard treatment for blood cancers1. However, utilizing the CAR approach to treat solid tumors has not been as successful because many of the surface antigens upregulated in solid tumor cells, and thus chosen as targets for CAR-T cells, are present at significant levels in normal tissues2. This has resulted in significant adverse effects in clinical studies including toxicity to healthy tissues and at worst, has proven fatal3. Methods for testing different models of CAR-T cells in vitro can provide further insight into viable antigen targets before first-in-man studies that utilize such models. The latest advancements in drug discovery screening, especially for cancer therapeutics, utilize three-dimensional (3D) cell culture models which more closely mimic the in vivo tumor microenvironment. For example, 3D multicellular tumor spheroids develop hypoxic cores, demonstrate gradients of various soluble factors, and a diffusion profile for drugs similar to tumors4. Here we demonstrate an HTS-compatible system to assay CAR-T cells against tumor spheroids by combining Corning® spheroid 384-well ultra-low attachment microplates, which enables the reproducible formation of a single spheroid in each well, and the DiscoverX KILR® Cytotoxicity assay, which provides a non-radioactive, dye-free method to specifically measure target cell death in a co-culture using luminescence…
Cell Harvesting – Selecting a technology compatible with cell density and feed turbidity
In this podcast and accompanying article, we interviewed Silke Bergheim-Pietza, Global Product Manager Depth Filtration, Pall. We discussed challenges faced in the cell harvesting step, in particular, selecting the best cell harvesting method based on the cell density and feed turbidity of the process and meeting the demand of increasing cell densities. Download the cell harvesting technology selection guide and use the guide to compare the latest single-use harvesting technologies...
Real-time Mycoplasma Contamination Detection for Biomanufacturing
Biomanufacturing contamination due to Mycoplasma is a very real concern, as it poses a potential health risk for patients. As such, regulatory agencies require biopharmaceutical companies to test for the presence of mycoplasma both during the manufacturing process and in the final product. While any contamination can be extremely challenging and costly, mycoplasma contamination is particularly difficult…
Addressing Challenges in Downstream Biomanufacturing with a platform purification approach
In this podcast and accompanying article, we interviewed Jonathan Royce, Business Leader, Chromatography Resins, GE Healthcare Life Sciences, about the biggest challenges in Downstream biomanufacturing including overcoming bottlenecks, changing antibody structures and bioburden control. Jonathan shared how a purification platform can address some of these issues and discusses purification challenges that still need to be resolved.
The Top 25 Downstream Column Blogs of 2017
I have compiled a list of our most popular 25 blogs, podcasts, and webinars for 2017 listed in alphabetical order…
Protein A Chromatography – A look at where we have been and where we are going
In this podcast and accompanying article, we interviewed Jonathan Royce, Business Leader, Chromatography Resins, GE Healthcare Life Sciences, about the evolution of Protein A including the latest developments in Protein A chromatography resins. We also discussed what the future holds for this purification mainstay and how it can continue to address the changing needs of biopharma…
Downstream Bioprocessing Cost Modeling – Looking at Integrated Continuous, Single-use and Stainless Steel Platforms
Process economics are frequently discussed with respect to continuous biomanufacturing implementation. More specifically, are the potential cost benefits worth making a manufacturing change and in which situations are the benefits greatest? At Biotech Week Boston in September, there was a very interesting talk titled “Cost modeling of the downstream bioprocessing design space,” presented by Mark Schofield, Ph.D., Senior R&D Manager, Pall Life Sciences. In the talk, Dr. Schofield shows data related to cost modeling the downstream bioprocess design space. He also describes some of the challenges facing biomanufacturing including cost pressure, competition, and the rise of biosimilars, and how implementing integrated continuous operations can address several of these challenges…
Webinars:
The Process Economics of Continuous Downstream Bioprocessing
New Webinar Available On Demand!
The cost of goods of an Integrated Continuous Bioprocessing (ICB) platform for the manufacturing of a mAb from fed-batch cell harvest has been evaluated using BioSolve Process, a modeling software from BioPharm Services. The costs associated with the ICB platform were compared to those of stainless steel and single-use batch processes. These downstream processes were evaluated across sets of clinical and commercial production scenarios. For both sets of scenarios, 27 different cases were modeled by varying 3 factors: bioreactor titer, volume, and number of batches per year. By taking this approach, the cost-benefits of the ICB platform could be seen across a wide range of manufacturing scales.
In this webinar, participants will learn:
- The findings of the full-factorial modeling exercise.
- The cost-benefits of continuous bioprocessing at many scales of manufacturing.
Podcasts:
Check out our podcast channel. We have 15 great podcasts covering drug discovery, stem cell culture, upstream and downstream biomanufacturing and more!
Click below to download through iTunes or Google play:
Headlines:
“How Cancer Immunotherapy Is Getting Even Better,” Time
“Last year, the Food and Drug Administration approved two new immunotherapies to treat certain leukemias and lymphomas. Now, in a study published in the New England Journal of Medicine, researchers detail who is most likely to benefit from the treatments, called CAR T Cell Therapy…”
“Sunovion Parkinson’s Drug Heads to FDA, Setting Up Battle With Acorda,” Xconomy
“Another drug that may help alleviate some of the debilitating symptoms of Parkinson’s disease is on its way to an FDA review, setting up a possible commercial battle between two drug developers, Sunovion Pharmaceuticals and Acorda Therapeutics. Sunovion, of Marlborough, MA, said late Monday that its experimental Parkinson’s drug, APL-130277, succeeded in a 109-patient Phase 3 trial. The drug helped improve the motor function of adult Parkinson’s patients suffering “off” episodes, meaning their medications aren’t working. Sunovion plans to file for FDA approval in the spring…”
“FDA agrees to quick review of smallpox drug,” Corvallis Gazette Times
“A Corvallis biotech firm is on a fast track toward approval of the world’s first treatment for smallpox. Siga Technologies announced on Wednesday that the Food and Drug Administration has accepted its new drug application for the oral formulation of Tpoxx, the company’s pill for treating smallpox infection, and has promised to complete its review in six months rather than the usual 10…”
“Abcam, Molecular Devices join forces to develop immunoassays for researchers,” FierceBiotech
“Abcam, a supplier of protein research material and kits, has teamed up with bioanalytical measurement solutions expert Molecular Devices to develop screening tools for the life science industry. The initial focus of this transatlantic collaboration is on creating new high-sensitivity fluorescent enzyme-linked immunosorbent assay (ELISA) kits. These immunoassays are used to detect and quantify substances such as peptides and proteins in basic research, high throughput screening and diagnostics…”
“Cobra Biologics and Symbiosis granted £1.9 million from Innovate UK,” EPM
“This grant will be used by the companies to establish commercial viral vector manufacturing capabilities within the UK as part of their joint investment project (costing £4.8 million in total). The whole project is aimed at developing world leading capabilities for clinical and commercial production of gene and immunotherapy viral vectors for both drug substance and drug product manufacturing. Additionally, it will support a larger investment in the production capabilities of both companies…”
“Corning and CytoSMART collaborate to simplify cell counting in laboratories,” News Medical Life Sciences
“Corning Incorporated and CytoSMART Technologies BV today announced an agreement that will simplify mammalian cell counting in laboratories around the world. Cell counting is a critical step in subcultivation in the cell culture workflow…”
“Bristol-Myers’ positive cancer data still lags Merck,” Reuters
“Bristol-Myers Squibb Co (BMY.N) on Monday provided some positive data on its immuno-oncology drugs for the most lucrative lung cancer market but it fell short of giving clarity on its ability to compete with a rival treatment from Merck & Co Inc…”