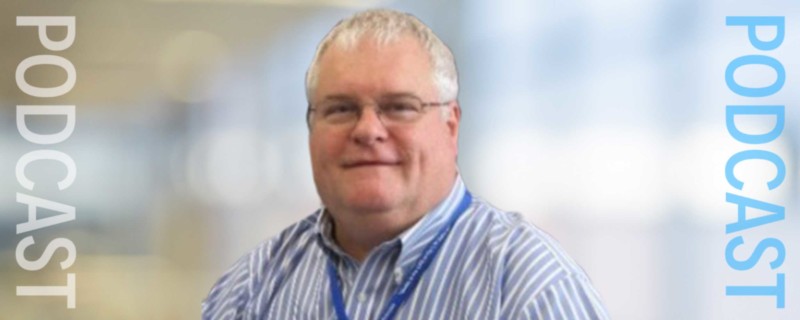
Integrating bioprocessing steps to improve efficiency and reduce cost
Podcast: Download (Duration: 8:32 — 11.7MB)
Subscribe Here: Apple Podcasts | Spotify | RSS | More
Subscribe to the Cell Culture Dish Podcast on: iTunes | Google Play
Show Notes
I began the interview by asking Dr. Morris to explain why the integration of processes is critical. He explained that in bioprocessing there are several different defined activities. Integration reduces the total number of separate activities and the amount of processing time. In addition, it reduces the amount of human interaction that is required, especially if a level of automation is involved.
Next I asked what challenges does integration aim to address. Rick described how the goal of integration is to control processing risks and reduce processing time to accelerate production. In addition, manufacturing costs should be reduced without compromise to quality or performance of the final product. Integration permits higher throughput from a fixed footprint and fixed resources. This allows greater flexibility and increases the capacity of manufacturing facilities.
I asked how to increase integration between upstream and downstream processing. He said that traditionally there has been a rigid divide between upstream and downstream, but that is beginning to change. When upstream optimizes cell culture to reach the highest titer, that often results in an increase in host cell protein and DNA contaminants. This has a significant impact on downstream, sometimes so great that it offsets any gains achieved in upstream. The way this has been addressed is to create beter and more efficient downstream processes. However this can be further improved by connecting various systems in upstream and downstream so that they work more in harmony.
Then we discussed how companies can utilize what is already in their facility and still increase integration. Rick said it really depends on what is currently in their facility. If they have already incorporated some single-use systems then they have the foundation for increased integration. There can be a mix and match approach where some continuous single-use modules are added. Even with a stainless facility, companies can connect to single-use modules to improve integration.
I closed by asking how integration facilitates moving from batch to continuous. He said continuous is the ultimate in process integration and we can look to other industries, like the automobile industry, to see examples of advanced integration and continuous processing. Biopharma is moving in this direction and has support from regulatory bodies to increase integration and continuous processing.
Lastly I asked if Rick had anything else he would like to add for listeners and he said that he feels integration is a very exciting area of technology and is constantly changing and evolving. Particularly exciting is the increase in the use of software for integration and automated antalytical control. These improvements are really shrinking the production platform and making it a mobile process.