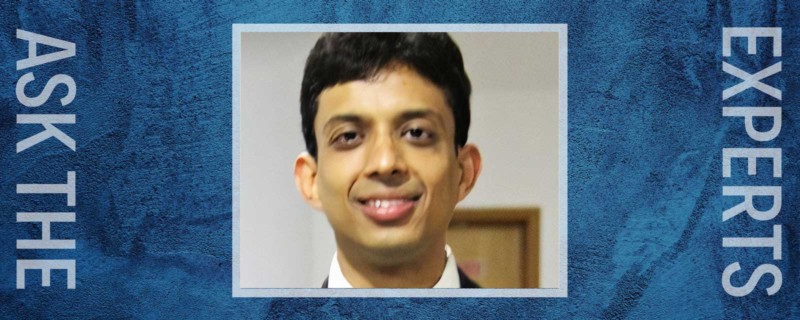
Smart Data Management and Advanced Analytics to enable Bioprocessing 4.0
Bioprocess 4.0 promises to be the next evolution of biomanufacturing and a critical aspect of implementation is the collection, management and analysis of large amounts of data from various sources. However, application of these principals has been challenging and biopharmaceutical companies are all moving at their own pace. The ability for companies to move toward a more platform approach has been hindered by incompatibility of various devices, data sources and software packages.
MilliporeSigma has developed its Bio4C™ Software Suite, and the browser-based Bio4C™ ProcessPad to address incompatibility issues and create an user friendly, digital ecosystem that allows biopharmaceutical teams to control, connect, collect and collaborate more effectively and efficiently. This approach to data management creates a central, validated source of information for process analytics, facilitating key activities such as monitoring, investigations, troubleshooting, reporting, data sharing and regulatory compliance.
With the complex issues surrounding digital data collection and analysis, it is important to seek out experts in the field who can answer questions about the implementation and capabilities. For this Ask the Expert Session, we asked Hemant Garg, Product Manager Analytics, MilliporeSigma to provide his expertise and answer reader questions.
Meet our Experts
Hemant Garg is on a digital mission to help the biopharmaceutical industry grow and evolve in a data-driven world. Trained as a business analytics biotechnology engineer, he has 14 years’ professional experience working across multiple roles within biopharma manufacturing. Hemant’s expertise in complex industry research, long-term forecasting, data analytics and process modeling enable him to identify, create, and capitalize on unmet market needs. At MilliporeSigma, Hemant leads the strategy and launch of digital and analytics products for biopharmaceutical customers and is presently working as a Product Manager Analytics in Integrated Solution Marketing, BioContinuum™ Platform.
Question 1
I am concerned about the training and cost of a more comprehensive data management system although I realize we need it. What is the simplest form of a data management system and can it grow with the company?
We have significantly reduced the training needs by creating a product with an easy and intuitive user interface thereby flattening the learning curve and speeding time to independent operation.
With our annual subscription model, customers can easily budget for the product without the need for a high upfront investment. Additionally, the design and deployment model of the product allows for increasing the scope in phases as the company’s needs grow.
The simplest form of data management in a manufacturing set-up would involve basic data aggregation capability in a validated manner and a set of statistical tools to do process analytics. This is enabled by the Bio4C™ ProcessPad Offline Module. This module also provides the ability to capture data from manual paper records in an electronic format. For large companies with systems like MES (Manufacturing Execution System), LIMS (Laboratory Information Management System), Bio4C™ ProcessPad can connect to these systems directly to fetch offline batch parameter data. In addition to offline data, if a company would like to add machine data visualization and analytics capability, they can add a Bio4C™ ProcessPad-RT module to add this functionality.
Question 2
How does this system interface with regulatory and manufacturing groups?
One of the key benefits of Bio4C™ ProcessPad is that it enables data sharing and collaboration within the organization. Since our product is browser-based and our license structure provides unlimited user access throughout the company, users from different groups such as process development, internal regulatory and manufacturing teams can easily share their data analysis and visualizations, insights, reports (APQRs, Campaign Reports, Process Summary Reports, Equipment Utilization reports) etc. with each other through the platform.
Question 3
We have been looking at another software solution, but it seems that there will need to be a lot of template creation upfront for reporting, etc. What does your set up look like and how long does it take to get it up and running?
Our product is designed and built by bioprocess engineers for bioprocess needs and workflows, hence templates for data reporting can be set-up very quickly through a simple user interface by the end-users directly. We provide comprehensive training to all end-users for template creation at the time of product deployment. Once you’re trained, you can manage template creation without any dependency. This process simply involves the selection of key process/analytical parameters that one would like to trend, analyze, and use for reporting purposes.
Question 4
What does bioprocess 4.0 involve and what are the advantages?
Bioprocess 4.0 is a lot about digitalization and how this concept can streamline the analysis and multidirectional communication of data—be it between equipment, among unit operations, or across groups and stages of development. The concepts behind Industry 4.0 is related with the “Fourth Industrial Revolution.” These concepts include—connectivity, intelligence, and flexible automation. Our Bio4C™ Software Suite within Biocontinuum™ Platform is a novel platform combining process control, analytics, and plant-level automation, which enables users to look across the entire manufacturing process versus individual operational units, giving biomanufacturers complete process control and deep insights.
Question 5
It seems a bit overwhelming to take on a fully integrated system. Can you do this in phases?
Our deployments for Bio4C™ ProcessPad is performed in three phases and is supported with services every step of the way.
Phase I consists of web form creation and capturing all offline datasets in these process forms.
Phase 2 involves connectivity to process equipment through data historians to fetch online near real-time sensor data.
Phase 3 involves integration with other data management systems such as LIMS (Laboratory Information Management System), QMS (Quality Management System) or MES (Manufacturing Execution System).
Question 6
Does implementation require time with facility offline?
No, implementation of our product Bio4C™ ProcessPad doesn’t impact manufacturing production. We understand the criticality of manufacturing operations and hence our deployment process is short, smart, and user-friendly. Most importantly there is no need for your facility to be offline during the entire deployment of the product.
Question 7
Our group is trying to include more detailed analytics in process optimization. How close to real time is this system in analyzing incoming data?
The Bio4C™ ProcessPad-RT module provides direct web-based access to streaming data from process equipment for real-time machine and batch data analysis. Process engineers have easy access to data to perform routine monitoring of batch profiles or process troubleshooting.
Our module collects the sensor data directly from process-equipment in near real-time for trending, reporting and process analytics.
All these process parameters can be monitored live on user-defined dashboard with the additional capability of monitoring process-excursions and process anomalies.
Question 8
Can your system support digital twin programs in cell culture operations? Mini bioreactors?
Intelligently combining process data from disparate data sources generated during batch execution into a single, contextual, integrated data source, Bio4C™ ProcessPad ensures process information is current, complete, and accessible throughout the product lifecycle.
Since the dataset from multiple data-silos is aggregated and contextualized in our platform, this dataset can further be leveraged for building mechanistic models in advanced analytics applications such as digital twins.
Question 9
Is this compatible with smart devices like AI?
Bio4C™ ProcessPad software is a data collection, visualization, and analytics platform that enables bioprocess monitoring, lifecycle management, reporting, investigations, and continued process verification (CPV). Our platform collects datasets from multiple disparate data management systems and serve as a single, contextual, and integrated data source.
A browser-based environment, our product can connect seamlessly with third-party API’s (application programming interface) for artificial intelligence applications such as smart devices.